What does the choice of an optimal winding core contribute to the result of a print job?
First of All
Winding cores are used to wind or unwind foils, papers or films, e.g. in the printing press. Cardboard winding cores are often used for this process. However, aluminium winding cores are an alternative because they save costs and provide process reliability.
The goal of an optimal winding process is a winding that is as uniform as possible. It should not have wrinkles and should possess sufficient and homogeneous strength for the further processing steps. Process interruptions during the winding process can be due to several issues, such as broken winding cores, deformed core ends, or narrowed core diameters. These interruptions disrupt the process and significantly increase production costs. Reject rates increase, which heightens the use of materials, and possibly, other follow-up costs.
Insufficiently coordinated parameters of the winding process often cause problems. These parameters can include web tension, the tension situation or the condition of the winding cores. They can affect both the winding process and the quality of the film winding. In many cases, winding cores made of aluminium instead of hard paper improve production efficiency. Using aluminium can lead to a significant reduction in costs for in-house further processing.
Why is that? Winding cores are exposed to different stresses in everyday production. These stresses encompass humidity and temperature, friction, and braking and acceleration torques. They also include pressure loads caused by the winding weight and tension as well as by clamping heads or clamping shafts. Additionally, the cores must have a surface that is uniformly smooth. This is crucial to avoid damage to the film material, prevent the formation of wrinkles, and ensure even winding results.
Hard paper cores are made of hygroscopic material, i.e. they absorb moisture from the environment or release it again.
A higher moisture content causes the sleeve to swell. When wound, the inner diameter shrinks and the core is often difficult to clamp again. In extreme cases, this can mean that material that has already been produced and is actually perfect has to be thrown away. On the other hand, if the moisture content of the core is too low, it can lead to a reduction in the outer diameter, causing the lowest layers of wrapping to loosen and the wrap to telescope.
Not only the dimension but also the stiffness of the sleeve is influenced by the moisture content. This can result in greater deflection and even breakage of the hard paper core. Hard paper cores therefore require constant humidity during use and storage, which often cannot be guaranteed even in internal processes. By using special aluminium core such as the INOMETA WinCore® winding sleeves, problems that arise in connection with moisture are completely eliminated.
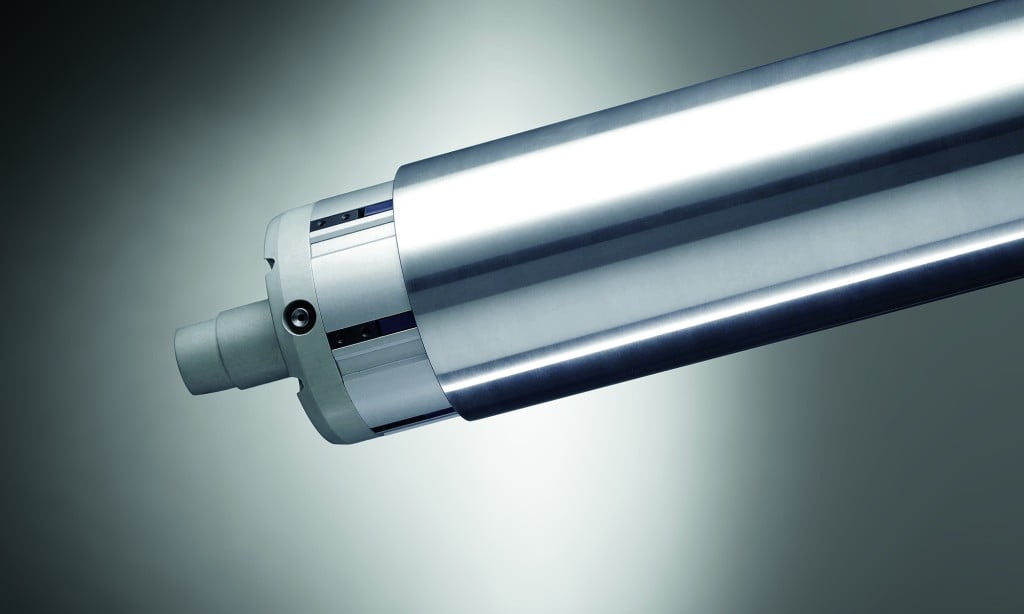
Another common cause of breakage of hard paper cores is excessive winding pressure.
The winding pressure is the sum of the winding weight and the transmitted web tension as well as the pressure from the contact rollers during the winding process. While the winding weight has a direct influence on process efficiency, the contact roller pressure and the optimal web tension are reflected in the winding quality. Aluminium cores have a significantly higher compressive strength.
Compressed cores and the associated problems, such as telescoping wraps, tensional cores and blocking of wrapping machines, can be quickly and easily avoided by using aluminium cores. Stable and constant processes are the rule when using aluminium sleeves.
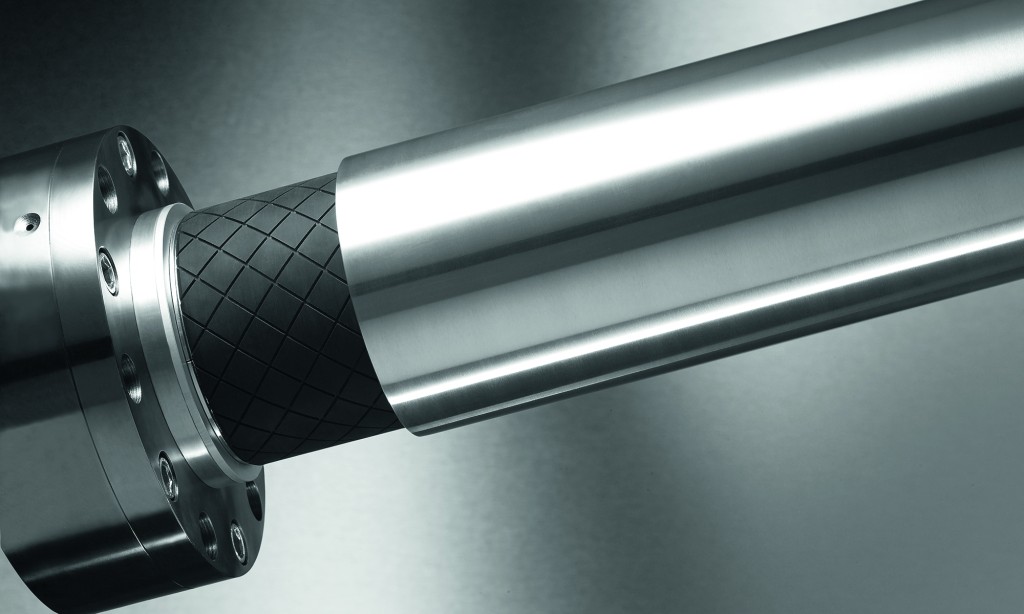
In Addition
They lead to further direct cost savings. Due to the significantly higher tensile strength of the material, significantly higher winding weights can be achieved with aluminium winding cores.
Aluminium cores also offer another important advantage. The deflection of the winding is generally lower than with hard paper cores. It is completely independent of fluctuations in humidity.
The deflection of the stretched, still stationary roll depends on several factors. On the one hand, it depends on the tensioning situation, i.e., the use of clamping heads or tension shafts. On the other hand, it also relies on the roll width to tube width ratio, the rigidity of the film material and tube, and the roll weight and wall thickness. Aluminium is ten to twenty times more rigid than standard hard paper cores. This increased rigidity means that the deflection of the wrap on an aluminum tube is comparatively lower in the same clamping situation.
With thin material, the unevenness in the contact surface of hard paper cores can’t be compensated for as well as with thicker material. It is deformed more easily. In addition to this, pressure is created on the lower layers of film. This pressure can especially damage pressure-sensitive films, even with slight deflection. Aluminium winding tubes can significantly reduce these problems and thus improve the overall winding quality.
In addition to the deflection, the concentricity of the core also influences the formation of wrinkles in the wrap.
On the one hand, an uneven outer diameter prevents the wrapping material from being laid down evenly, which can result in air pockets and wrinkles. On the other hand, the winding core does not rotate evenly, preventing constant material tension across the entire winding width. WinCore® aluminium winding cores from INOMETA are finely aligned with a concentricity of max. 0.2 mm/m, which cannot be achieved by conventional hard paper cores due to production reasons. WinCore® winding cores from INOMETA enable less wrinkling, an improvement in winding quality and thus a reduction in rejects.
In addition to further process improvements such as fewer roll changes, fewer remaining layers, lower core requirements and high process stability, aluminium cores can be used for several years because, unlike cardboard cores, they can be reused several times – up to 1,000 times or more.
The material-related higher acquisition costs are usually paid off within a few winding processes thanks to the process savings and the hard paper cores saved. WinCore® aluminium winding cores from INOMETA thus contribute to cost and process efficiency in internal film production and processing. In addition, the WinCore® winding cores contribute to economic sustainability thanks to their significantly extended service life and the wide range of possible uses.
For further inquiries or quote requests, please fill out the form to receive information.