Flexo printing, commonly used for packaging and labels, requires precision. Accurate platemaking is critical to ensuring that the final prints match the designer’s vision. Two critical factors in flexo process are elongation and distortion.
Understanding Elongation in Flexo Platemaking
Elongation occurs when the soft flexo plate wraps around the impression cylinder. This action stretches images, halftones, and text across the curved surface. Without compensation, printed images will not match the original design. For example, a circular image may print as an oval, and vertical lines may undergo stretch. This distortion can seriously affect the quality and accuracy of the printed product.
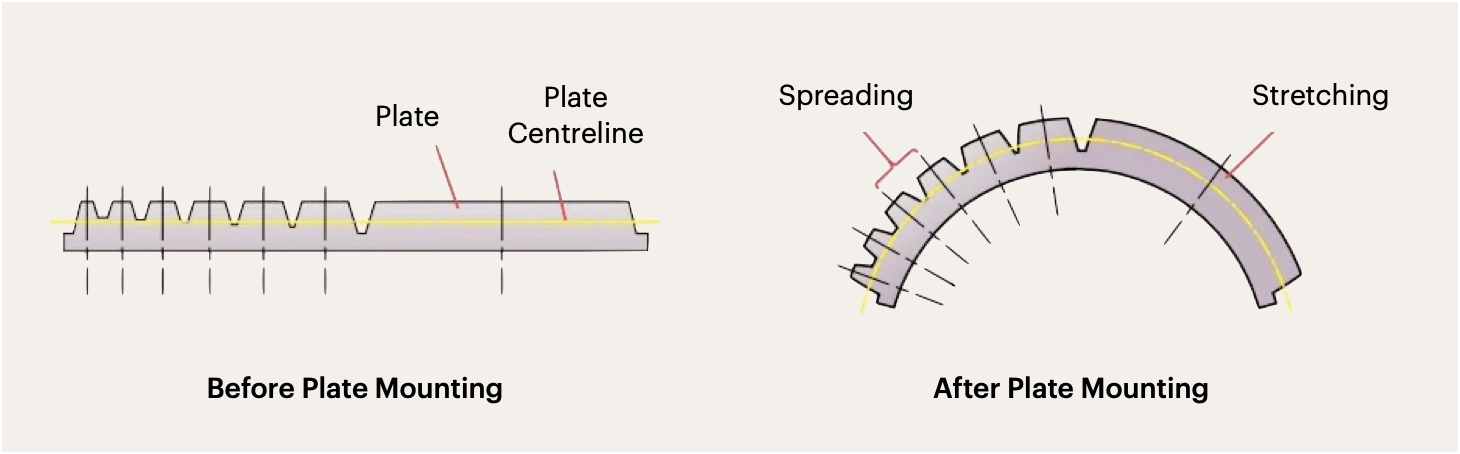
The physical properties of the plate contribute significantly to this phenomenon. The flexibility of the plate material, combined with the tension applied during the wrapping process, changes the dimensions of the design elements. As a result, careful adjustments must be made to counteract this effect and ensure that the integrity of the original layout is maintained in the final printed image.
Distortion: Counteracting Elongation
Distortion in flexo platemaking involves pre-adjusting the image to counteract the elongation effect. This process typically takes place in the flexo software or at the RIP (Raster Image Processor) stage before imaging the film. The amount of distortion required depends on several factors: the plate thickness, the mounting tape used, and the circumference of the cylinder (known as the repeat length). Thicker plates and shorter repeat lengths typically result in more distortion.
A basic formula usually guides the stretching process, adjusting the image dimensions to exactly match the final printed output. This calculated adjustment ensures that when the plate is wrapped around the cylinder, the stretched image will print correctly. In essence, distortion is the deliberate manipulation of the digital image to pre-compensate for the physical stretching that occurs during printing.
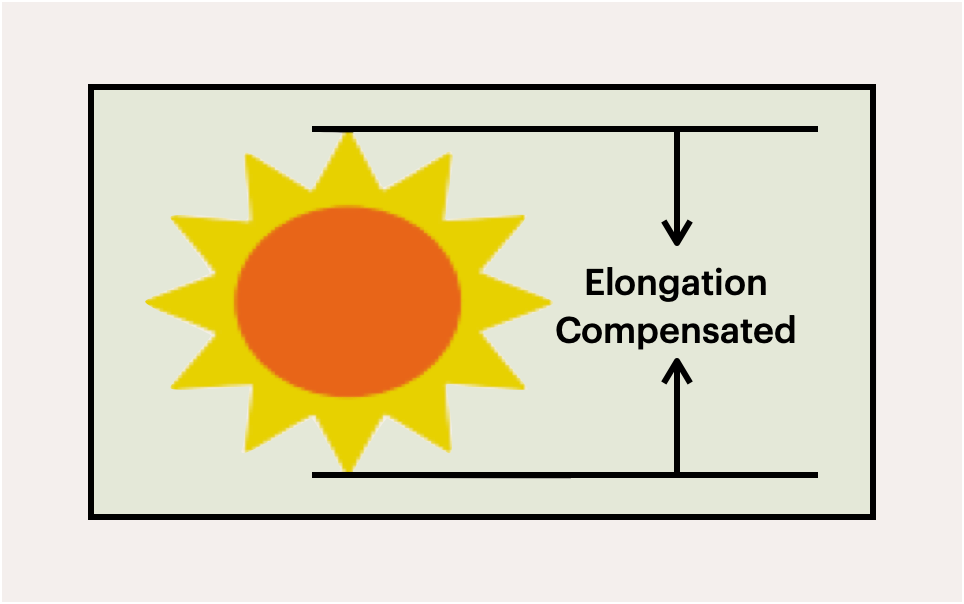
For instance:
– The artwork dimension measures 12″ by 12″.
– If the plate will be elongated by 20% after being mounted, the elongation rate is 120%. Thus, the distortion rate should be its reciprocal – 83.33%.
– The image should be distorted to compensate for plate elongation. While the traverse dimension stays 100%, the dimension along the curve should be 12″ × 83.33% = 10″.
Printers often initially rely on trial and error techniques to calibrate the correct levels of compensation. This involves printing test runs and making iterative adjustments until the desired output is achieved. However, this method can be time consuming and resource intensive.
Digital Tools for Calculating Proper Distortion Rates
Modern flexo printing uses advanced digital tools to effectively manage distortion. The process begins with measurement of plate and cylinder parameters, which the software uses to adjust the image. Then, predictive algorithms take into account factors such as plate material, cylinder circumference and plate thickness to pre-distortion the image and compensate for elongation as the plate wraps around the cylinder. By simulating the behaviour of the plate on the cylinder and making the necessary adjustments to the digital file, these tools ensure accurate printing.
This approach prevents problems such as stretched text or misaligned graphics, resulting in high-quality prints that meet design specifications. Precise distortion management significantly improves the accuracy and quality of flexo prints. By using these specialised tools and software, printers can produce results that closely match the original designs, improving the overall effectiveness of the printing process.
Conclusion
Effectively managing elongation and distortion in flexo platemaking is critical to achieving high quality prints. By understanding and compensating for these issues, printers can ensure that the final product meets design expectations. With the help of modern software and precise techniques, achieving accurate and consistent flexo prints is much more achievable.