Recent trends and challenges in the flexo printing industry have led to a shift from digital round top dot plates to flat top dot plates with surface screening. This article would navigate you trough the questions of what Flat Top Dot technology is, what has caused the shift to surface screening, and what the benefits are.
Background: Trends in Flexo Industry
In order to improve the OEE (Overall Equipment Effectiveness) of printing presses, more standards such as ECG (Extended Colour Gamut) with 7 colours have become trendy. The effects of ECG are many. For example, printing in standard colours only reduces ink costs. Fewer ink changes mean fewer cleaning cycles and press downtime. ECG sounds simple, but it also requires standards for the printing plates to ensure proper reproduction of the design and high consistency of the print.
Another trend is to use more recycled materials or lower grade substrates that have higher tolerances. The higher thickness tolerances or substrate naturally affect the ink lay-down, resulting in pin-holing in the worst case. Compensation for pin-holing has often been through higher print pressures, resulting in other unwanted side effects such as dot bridging, haloing, and trailing edge voids. None of this is pretty, but it is simply due to the erased print form.
How Flat Top Dot Plates with Surface Screening Help?
Increasing the print quality and reducing the total cost of printing is probably the everlasting trend not only in the flexo printing industry.
An essential part of helping and advising is done by the repro house that provides the plates to the printer. Köstlin, a German repro house, did a comparison of the three main technologies available on the market. Standard digital plates, flat top dot technology plates, and flat top dot technology with surface screening. The setup was the same for all three types of printing, such as ink, repeat length, print speed, etc.
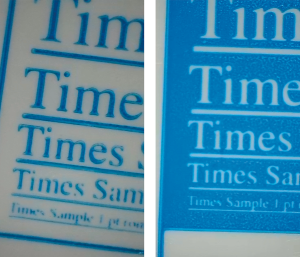
No Surface Screening
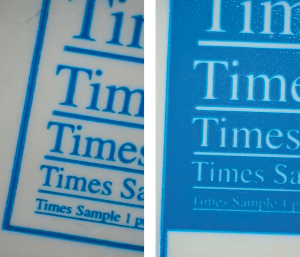
No Surface Screening
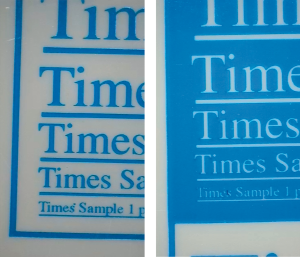
UV-Optimised Surface Screening
The flat top dot technology plate already shows an improvement over the standard round top dot. The main driver for the improved results is that with FTD (flat top dot) all the print elements are at the same height when viewed from the cross section. Round top dots plates have generally lower dots compared to full tone areas as the dots “shrink” during the washout process. Round top dot plates therefore generally require more printing pressure to achieve an even printout.
The surface screening on the FTD plate then allows better distribution of the ink on top of the plate. The little micro cells carry the inks nicely and release it to the substrate. Surface screening reduces the amount of ink (cost saving) and enhances the ink lay-down (quality improved). All unwanted side effects such as halo, trailing edge void and dot bridging are significantly reduced due to the lower printing pressure in the printing nip.
Why not move completely to FTD with surface screening?
The selection of the right printing plate and the best fitting surface screening is essential to be successful. The mindset needs to change that FTD plates are only for high quality applications. Even simple corrugated line work or full tone prints can have significant improvement with the right surface screen as the ink lay-down is more homogeneous and the side effect is a reduction in ink consumption. The slightly higher plate price is paid off by the savings on press.
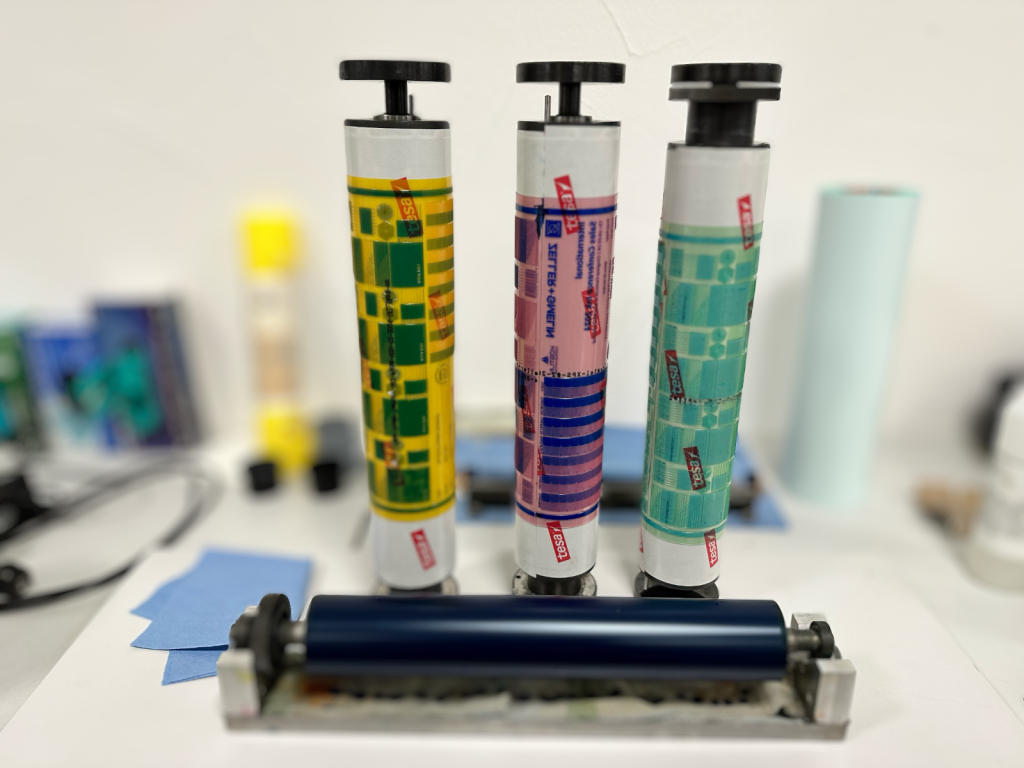