Achieving high-quality prints in flexo printing relies heavily on the quality of the flexo plates used. Technicians must possess a thorough understanding of the common technical issues that can arise with flexo printing plates and the appropriate solutions. This article is part 3 of flexo plate troubleshooting series that explores some of the most frequently encountered problems, their causes, and the technical solutions to overcome them.
Blocking
- Problem: Ink transfer from one print to the next.
- Causes: Ink drying problems, web tension issues, or substrate humidity problems.
- Solutions: Optimise ink, substrate, and dryer parameters.
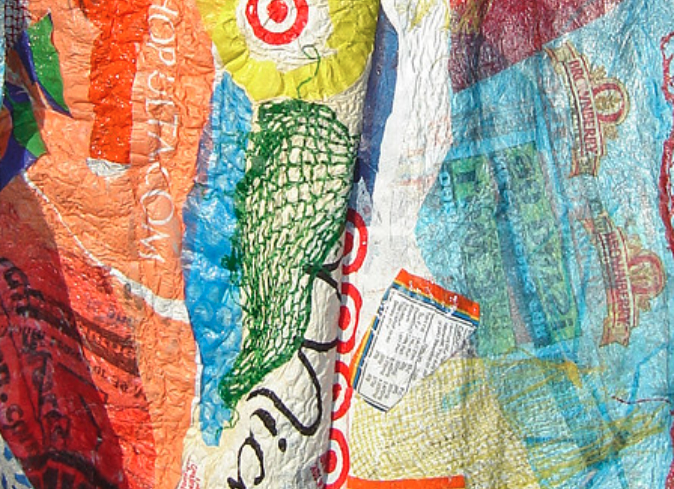
Ink Splashing
- Problem: Ink splashing.
- Causes: Low ink viscosity or incorrect anilox specification (high volume or low line count).
- Solutions: Adjust ink viscosity; optimise anilox specification.
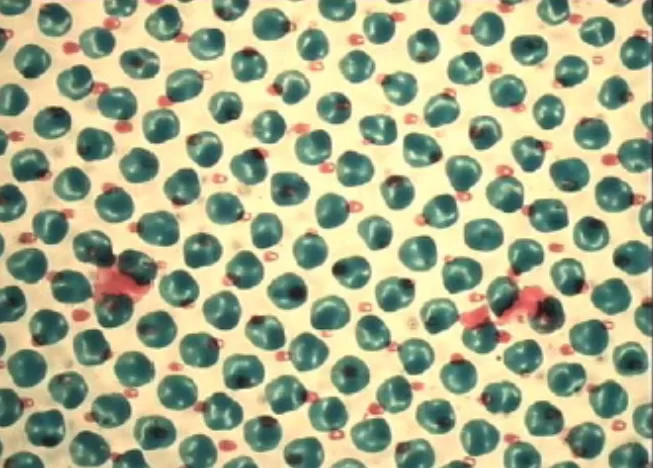
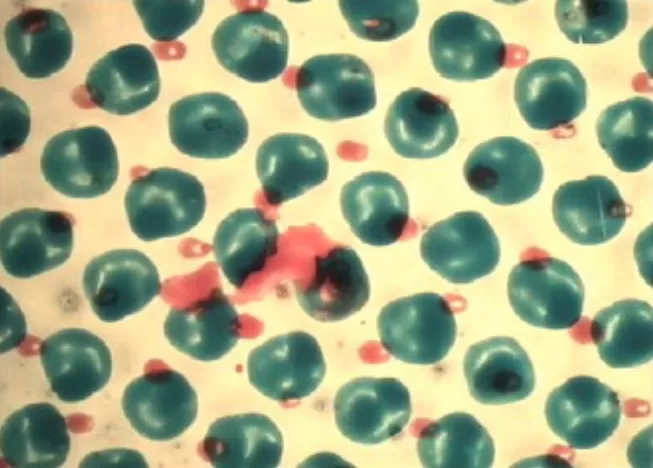
Misregistration
- Problem: Misalignment in print registration.
- Causes: Plate mounting issues, equipment problems during plate making, plate orientation on imaging system, or separations from different raw material batches.
- Solutions: Ensure plate making equipment functions correctly; image separations consistently; use plates from the same batch.
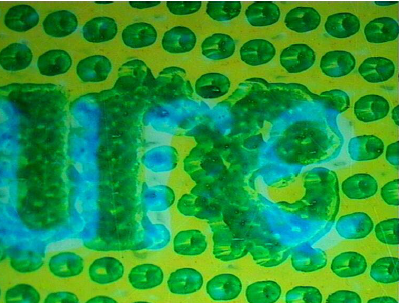
Element Edges Start to Print Early
- Problem: Element edges print prematurely.
- Causes: Cupping issue or high impressions between anilox and plate or plate and substrate.
- Solutions: Optimise plate making parameters (e.g., dry times); adjust impression settings on press.
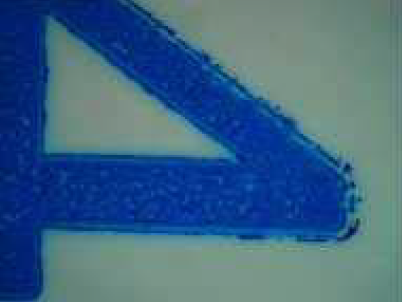
Unsharp Printing
- Problem: Blurred printing with high dot gain.
- Causes: Plate swelling from unsuitable solvents/cleaners causing softening during printing, high impression settings, cupping issue, or ink issues.
- Solutions: Use appropriate solvents; reduce impression settings if necessary.
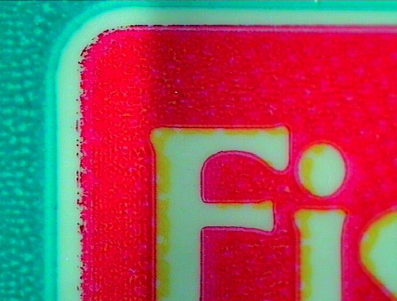
Ink Transfer Issues
- Problem: Poor ink transfer.
- Causes: General ink issues, ink drying on anilox roller, or plate surface contamination.
- Solutions: Check ink condition; clean plate surface and anilox roller.
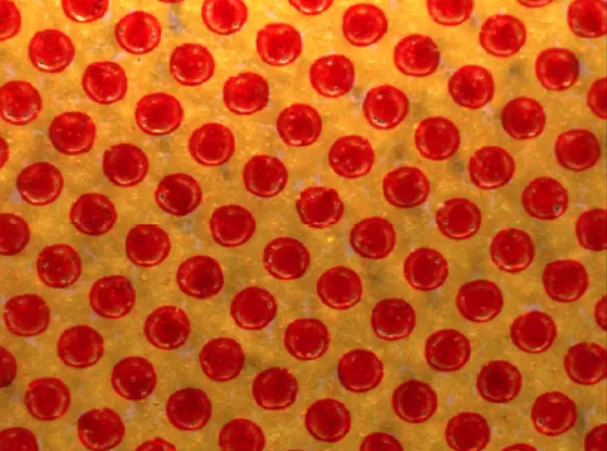
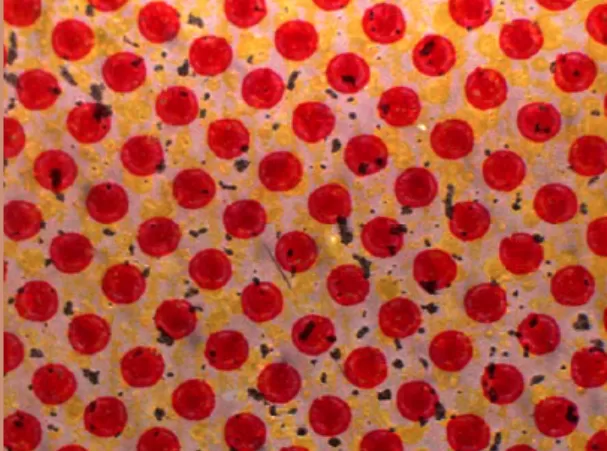
Filling-In of Fine Elements
- Problem: Fine elements filled with ink.
- Causes: High anilox to plate impression or incorrect ink viscosity.
- Solutions: Confirm anilox settings; adjust ink viscosity as needed.
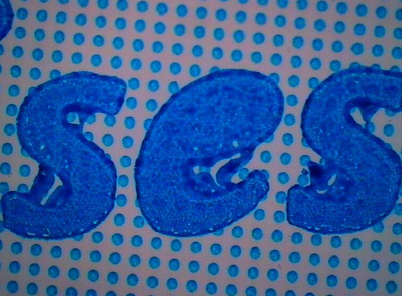
Ink Bleeding
- Problem: Ink bleeds, obscuring screen structures.
- Causes: Improper pigments in ink or pH imbalance in water-based ink.
- Solutions: Consult with your ink manufacturer.
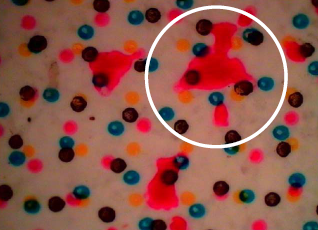
Dirty Print in Transitions of Flexo Plates
- Problem: Dirty printing in screen transitions.
- Causes: High anilox to plate impression, low ink viscosity, high anilox volume, or shallow intermediate depths or plate relief.
- Solutions: Optimise press and ink parameters; correct plate making issues.
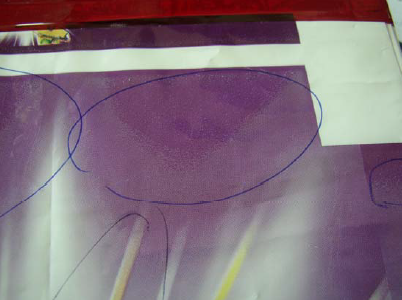
By familiarising themselves with these common issues and their respective solutions from part 3 of flexo plate troubleshooting series, technicians can effectively fix flexo printing plate and maintain high-quality print results. Stay tuned for Parts 1 and 2 of this series, which will delve into additional problems and their remedies.