This blog was written and submitted to us by Torben Wendland
The back exposure of a flexo photopolymer printing plate is creating the base (or floor) of the plate. The height difference between plate surface and floor defines the relief depth.
Which factors are influencing the relief target?
The required relief depth is depending on several factors. All of them are leading to a target relief depth:
- Print application and substrate: Typically, print applications which require less impression (e.g. narrow web) can use a minor relief depth compared to applications with higher impression or uneven substrates (e.g. corrugated post-print).
- Plate type and thickness: On thicker plates, relief depths of several millimetres are common. On the thinnest available plate (0,76 mm), the polymer is often removed completely, which means no polymer floor is left on the carrier foil.
- Design elements: Finally, the relief depth is also influencing the ability to anchor elements on the plate. At a lower relief depth, it is possible to stabilise smaller elements like finer dots or lines.
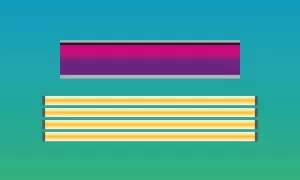
How to determine the back exposure length?
To achieve the correct floor thickness, it is necessary to adjust the back exposure length. Typically, a step test determines this exposure time. You expose various steps at increasing exposure times on the same plate. Each step increases the exposure length by a set increment (usually 3-5 seconds for thin plates, 10 or more seconds for thick plates). After fully processing the plate, you find a “staircase” of different floor heights on it. Measurements of these steps’ heights with a thickness gauge help to determine the necessary back exposure length based on the results.
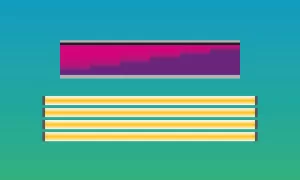
How to conduct the back exposure in practice?
Temperature affects the light intensity of the UV-A tubes. Therefore, before beginning the back exposure or conducting a back exposure test, preheating the tubes is advisable to ensure consistent relief depth with previously tested results.
The back exposure process for a flexo printing plate varies slightly with the type of exposure equipment used. When the light source is in the machine’s lid, it is necessary to flip the plate over to conduct the back exposure. With glass bed exposure units where the light comes from below, flipping isn’t necessary. In this case, you typically perform the back exposure right after imaging, in combination with the main exposure.