In the dynamic world of flexographic printing, achieving high-quality prints with maximal efficiency hinges significantly on the choice of components used in the printing process. Among these components, flexo doctor blades have been a staple in printing for numerous years. They stand out for their critical role in ensuring uniform pressure application to remove surplus ink effectively from the surface of an anilox roll. Thence, the ink film thickness applied to the printing plates or cylinders is metered. So, how to choose the right doctor blade for your business?
Variables in Choosing Flexo Doctor Blades
No printing setup is complete without a doctor blade, as the quality of your printing work heavily relies on it. However, when it comes to the selecting the right doctor blades, a few factors are at stake. The variation in materials, edge profiles, and thicknesses of these blades means that selecting the right type can substantially impact your print quality, production speed, and operational costs. This article delves into the factors that make certain flexo doctor blades more suitable for specific business needs.
Material Consideration
Flexo doctor blades are manufactured from a variety of materials, each offering distinct advantages and suited for different printing conditions. The most common materials include steel, plastic, and composite materials.
- Steel Blades
These are highly favoured for their precision and durability. Steel blades, particularly those made from high-quality, corrosion-resistant steel, offer excellent wear resistance and are ideal for long runs. However, they require careful handling due to safety concerns and potential damage to the anilox rolls if not used correctly.
- Plastic Blades
Plastic doctor blades are a cost-effective option that provides good performance with minimal risk of damaging the anilox rolls. They are best suited for applications where edge quality is less critical or when printing on delicate substrates.
- Composite Blades
Composite blades, made from a blend of materials, offer a balance between the durability of steel and the safety of plastic blades. They are designed to provide high-quality printing results while reducing the risk of anilox roll damage. Composite blades are becoming increasingly popular for businesses looking for versatility and performance.
Edge Profiles
The edge of the doctor blade plays a pivotal role in how efficiently it meters ink. The most common edge configurations are straight, bevel, and lamella.
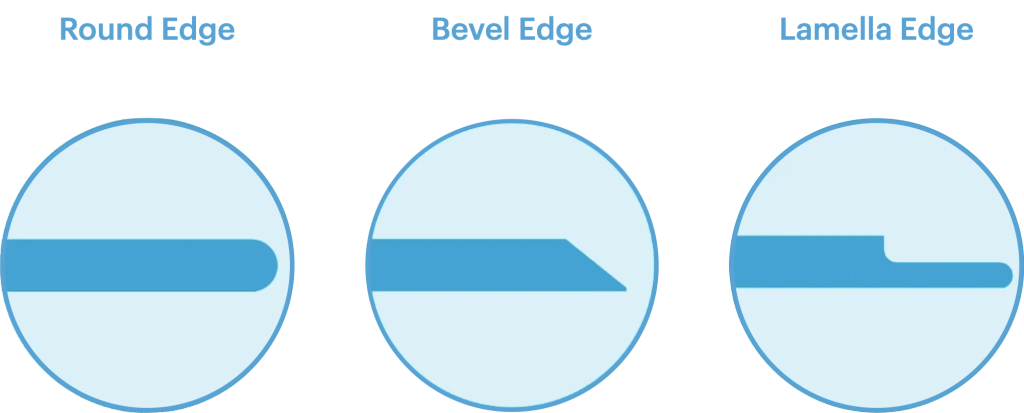
- Round Edge
A double-sided radius edge is simple but effective for many standard printing tasks. It provides a high quality seal and is best used in situations where ink film thickness variations are less critical.
- Bevel Edge
Beveled blades offer a sharper contact point with the anilox roll, allowing for a thinner ink film. This configuration is preferred for finer print jobs requiring higher resolution.
- Lamella Edge
Lamella, or stepped, edges provide the most precise metering by offering a consistent, thin ink film. This type of blade is ideal for high-end printing applications where print quality cannot be compromised.
Thickness Configuration
The thickness of the doctor blade is crucial for its flexibility and the control it offers over the ink film thickness. The thickness of common doctor blades ranges from 0.150 to 0.500 mm.
Thinner blades can conform more easily to slight irregularities on the anilox roll surface, allowing for a more uniform ink film. However, they may wear out quicker than their thicker counterparts, especially when used at high speeds or with abrasive inks. In contrast, thicker blades offer durability and resistance against wear but may not provide the same level of precision in ink metering, particularly on lower line screen anilox rolls.
Understanding Your Printing Requirements
Identifying the right flexo doctor blade for your business begins with a clear understanding of your specific printing needs. Factors such as the type of substrates you print on, the speed of your press, the intricacy of your graphics, and your print quality standards all influence the blade selection. High-speed presses with demanding print quality standards might benefit from durability and precision of lamella-edge composite blades, while a business focusing on straightforward jobs might opt for the simplicity and cost-effectiveness of straight-edge plastic blades.
Vendor Support and Blade Life
Choosing a reputable vendor can greatly affect your satisfaction with doctor blades. Quality blades from a dependable supplier mean consistent performance and fewer unexpected blade changes, increasing operational efficiency. Additionally, understanding the expected life of different blade materials and configurations can help you estimate operational costs accurately and plan for replacements in your maintenance schedules.
Conclusion
The right flexo doctor blade can enhance your printing process, impacting everything from print quality to production cost. By carefully considering material, edge profiles, thicknesses, and aligning these with your specific printing requirements, you can select a doctor blade that not only suits your current business needs but also supports your goals for quality and efficiency. Remember, the effectiveness of a flexo doctor blade is not solely in its design but in how well it matches the unique demands of your printing operations.