In today’s fast-paced printing industry, time is a crucial asset. Flexographic printers, tasked with delivering precision at scale, are under increasing pressure to manage shorter runs, quicker turnarounds, and diverse designs—all while maintaining consistent quality. Enter quick-change systems, a transformative solution for reducing downtime and optimizing productivity.
These innovative systems are tailored to meet the needs of modern flexography by enabling rapid plate changes, sleeve replacements, and anilox roll swaps, making them essential tools for businesses striving to stay competitive.
Understanding Quick-Change Systems
Key Features of Quick-Change Systems
Quick-change systems are designed with efficiency in mind. Their hallmark features include:
- Tool-Free Mechanisms: Allowing for seamless part replacements without specialized tools.
- Pre-Registration Technology: Ensuring precise alignment before the press even begins running.
- Automated Adjustments: Streamlining the setup process for enhanced accuracy.
How Quick-Change Systems Work
By incorporating modular components, these systems simplify the steps required to switch plates, sleeves, or rolls. For example, plate cylinders may have lock-and-go systems, where operators can secure and release components with minimal effort.
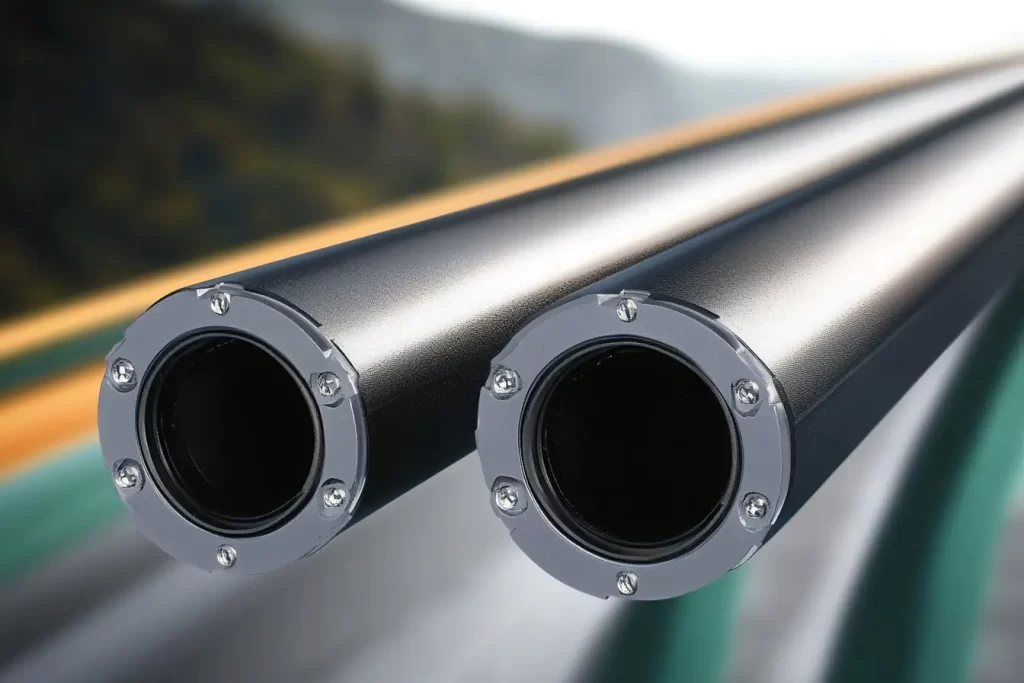
Benefits of Quick-Change Systems
Enhanced Efficiency in Flexography
Quick-change systems significantly reduce the time spent on job setup and changeovers, making it possible to handle more orders in less time.
Reduced Downtime and Improved Productivity
With fewer manual steps involved, printers can transition from one job to the next swiftly, minimizing production halts.
Applications of Quick-Change Systems
Packaging Printing
Quick-change systems are invaluable for printing packaging materials where frequent design changes are common.
Label and Film Printing
In high-demand sectors like labeling, where accuracy and variety are crucial, quick-change systems ensure seamless transitions.
Specialty Printing Applications
For intricate designs and custom jobs, these systems provide the flexibility to meet unique printing requirements.
Types of Quick-Change Systems
Tool-Free Plate Changes
These systems eliminate the need for tools, allowing operators to swap printing plates in a matter of seconds.
Quick Sleeve Changes
Quick-change sleeves make it easier to adjust press configurations for varying print widths and designs.
Automated Anilox Roll Changes
Automation ensures consistent quality by enabling fast and precise anilox roll swaps.
Key Components of Quick-Change Systems
Modular Plate Cylinders
These allow for easy plate removal and installation, reducing setup times.
Lock-and-Go Mechanisms
Securely fasten components without requiring time-consuming manual adjustments.
Precision Registration Controls
Advanced systems ensure perfect alignment, reducing the need for test prints.
How Quick-Change Systems Optimize Workflow
Faster Job Turnaround
By cutting down on preparation time, quick-change systems enable printers to meet tight deadlines with ease.
Streamlined Make-Ready Processes
Operators can set up new jobs with minimal effort, ensuring the press runs efficiently.
Challenges in Implementing Quick-Change Systems
Initial Costs and Training
Although the upfront investment can be substantial, the long-term savings and productivity gains make it worthwhile. Proper training ensures that operators can maximize the system’s benefits.
Compatibility with Existing Equipment
Choosing a system that integrates seamlessly with your current setup is critical to avoiding operational disruptions.
Advancements in Quick-Change Systems
Integration with Smart Technologies
Modern systems are incorporating IoT and AI capabilities, allowing for predictive maintenance and real-time performance monitoring.
Eco-Friendly Upgrades
Sustainability is a growing focus, with designs that reduce material waste and energy consumption.
Environmental Benefits of Quick-Change Systems
Waste Reduction in Printing
By minimizing errors and the need for test prints, quick-change systems help reduce substrate and ink waste.
Energy Savings
Efficient operations consume less energy, contributing to a smaller carbon footprint.
Conclusion
Quick-change systems are revolutionizing the flexographic printing industry by reducing downtime, improving productivity, and ensuring consistent quality. From tool-free plate changes to automated anilox roll swaps, these systems empower printers to tackle the demands of modern markets with confidence.
By investing in the right quick-change system, businesses can streamline their workflows, enhance efficiency, and ultimately stay ahead of the competition. As technology continues to evolve, quick-change systems will remain integral to the future of flexographic printing.
FAQs
What is a quick-change system in printing?
Quick-change systems are tools and mechanisms that allow for rapid component changes, reducing setup times in printing operations.
How do quick-change systems benefit flexographic printing?
They enhance efficiency, minimize downtime, and support faster transitions between print jobs.
Are quick-change systems compatible with all flexographic presses?
Most systems can be adapted to modern presses, but compatibility with older models may vary.
What types of components can quick-change systems replace?
They can handle printing plates, anilox rolls, sleeves, and more, depending on the design.
Do quick-change systems require special training?
Basic training is recommended to ensure operators use the systems efficiently and safely.
What is the ROI for quick-change systems?
While initial costs can be high, the reduction in downtime and waste often leads to significant long-term savings.