Printing has evolved into a complex interplay of technology and craftsmanship, with the Raster Image Processor (RIP) sitting at the heart of this technological symphony. By translating digital designs into printable bitmap images, RIPs ensure that what you see on screen actually comes to life on paper. This article aims to demystify the crucial role of the RIP and its software solutions in flexo printing process.
RIP and Screening in Prepress Stage
In the prepress stage of flexo printing, setting up a competent workflow takes centre stage. Specialist approaches tailored to specific processes ensure that the subsequent print run is a success. Both RIP and the finesses of screening are critical in optimising this prepress process, laying the groundwork for superlative printing results.
Decoding RIP
To the uninitiated, the term Raster Image Processor may sound mysterious. An RIP is a digital craftsman who translates the language of computers into a meticulous pattern of dots, each carefully orchestrated for the printing process. Think of the age of vector graphics, where scalability without loss of quality is the order of the day, thanks to a mathematical foundation rather than a reliance on pixels. But to transfer these sharp images to a physical medium, the magic of the RIP is pivotal. It rasterises or converts the graphics into contones or bitmaps – highly detailed, pixel-based images that are essential for high-quality printing.
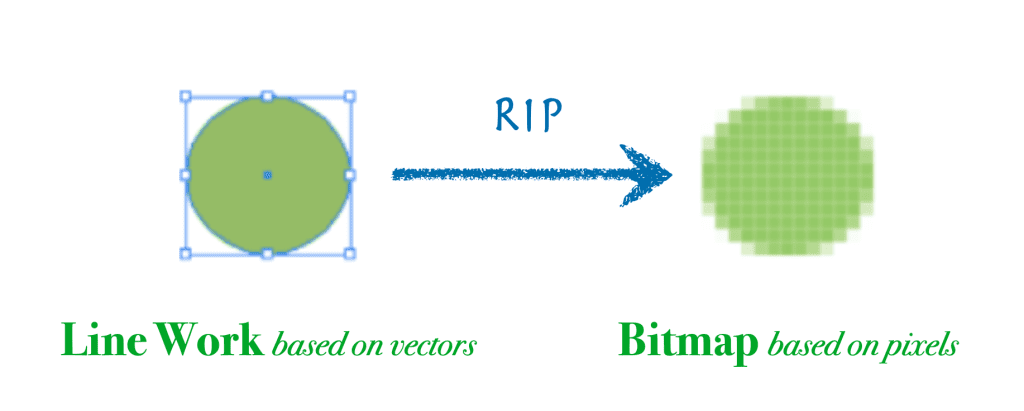
The Art of Screening
Screening is like the careful selection of ingredients that determine the flavour of a dish. The optimal screen depends on a number of components: the RIP itself, platemaking nuances, press configurations and the substrate. The anilox rollers play a starring role, as their characteristics limit the screen ruling that can be achieved. In terms of technology, the choices range from traditional Amplitude Modulation (AM) and Frequency Modulation (FM) to the avant-garde hybrid screens, each with its own merits. Hybrid screens are particularly intriguing because of the fine balance between dot stability and visual grain. A larger dot diameter provides stability but at the cost of increased grain.
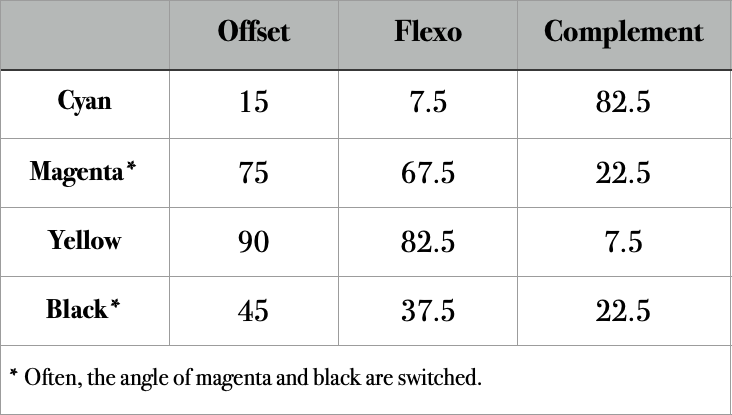
Flexo angles further complicate this dot dance. Flexography requires screen angles that are different from offset to prevent interference with the anilox roller pattern. These bespoke angles ensure that the final print is free of moiré patterns, contributing to a cleaner, more visually pleasing result.
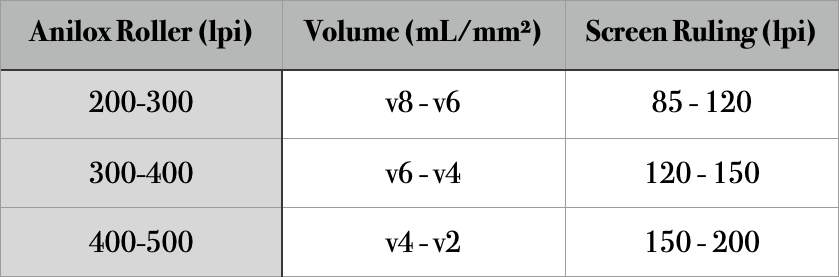
A Look at Flexo RIP Software Solutions
While the focus on RIP and screening is critical, it’s also important to highlight, albeit to a lesser extent, the software solutions that contribute significantly to the success of flexo printing.
Esko‘s Imaging Engine is one such solution, built on the robust foundation of Adobe’s PDF Print Engine. It offers impeccable colour management and screening, and works seamlessly with Esko’s Automation Engine.
An interesting option is Xitron‘s Navigator RIP, which presents its HXM screen for offset applications, but is adaptable to flexo when combined with advanced dot technologies. For flexo applications, Navigator’s ThermoFlexX hybrid screens are recommended, demonstrating the solution’s flexibility.
Finally, there’s StudioRIP, which is compatible with a range of image formats and designed for high-end output devices such as platesetters and imagesetters. StudioRIP’s all-in-one design sets it apart and ensures a streamlined, conflict-free experience.
Juxtapose these software solutions and each carves out its own niche. Esko’s solution is a powerhouse because of its integrative features, while Xitron’s bespoke renders adapt fluidly to flexo needs. StudioRIP answers the call for those looking for an all-in-one package without the need for additional plug-ins.
Conclusion
The careful selection of RIP and screening processes forms the backbone of high quality printing. Alongside the right software solutions, these tools become the unsung heroes of the printed page, transforming images from digital spectres into tangible masterpieces. By understanding and harnessing this powerful duo, the printing industry continues to adapt and thrive in an age where precision is not only desired, but required.