In flexographic printing, technology plays a critical role in ensuring high-quality output and efficiency, especially when it comes to the variety of substrates and colors involved in packaging. One of the standout systems contributing to this innovation is the stack press system. Widely adopted by the packaging industry, stack presses have become an essential tool for delivering consistency, precision, and flexibility in printing applications.
Whether you are a printer, a designer, or part of a production team, understanding the workings of stack press systems can be transformative for your business. This article delves into what makes stack press systems unique and how they contribute to the overall success of flexographic printing.
What are Stack Press Systems?
In flexographic printing, the configuration of the press determines how colors and images are applied to the substrate. Stack press systems are characterized by their vertical arrangement of print stations. Each station corresponds to a different color, typically following the CMYK model, although more colors can be added if needed.
The design of these systems allows for multiple colors to be printed in a single pass, which not only speeds up production but also maintains the precision necessary for high-quality packaging. In stack presses, each color unit is stacked one above the other, forming a vertical column, hence the name “stack press.” This vertical design distinguishes stack presses from other configurations such as central impression (CI) and inline presses, offering unique advantages for specific applications.
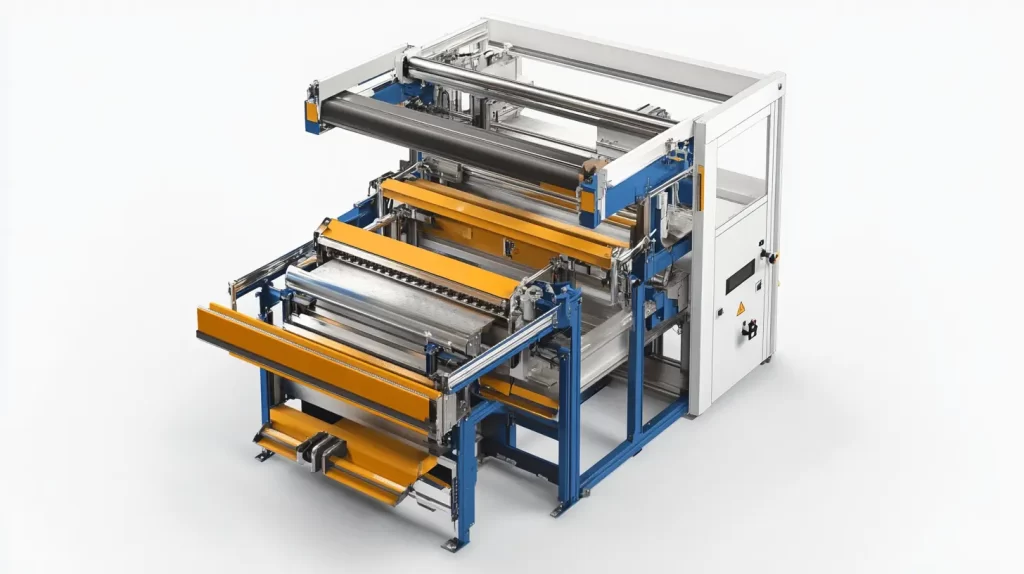
Key Features of Stack Press Systems
Stack press systems offer several unique features that make them particularly well-suited for certain types of printing jobs. Here are some of the standout features:
1. Vertical Configuration:
The hallmark of the stack press is its vertical design. This arrangement allows for easy access to each print station, making it convenient for operators to monitor and adjust the press as needed. This accessibility contributes to maintaining the quality of the print job.
2. Multiple Print Stations:
Stack presses can accommodate anywhere from two to eight color stations, depending on the model. This versatility is ideal for jobs requiring more complex color schemes or special effects such as metallic inks or varnishes.
3. Substrate Versatility:
One of the biggest advantages of stack press systems is their ability to handle a wide range of substrates. Whether you’re printing on film, paper, or plastic, stack presses offer the adaptability needed to accommodate various packaging materials.
4. Modular Design:
Stack presses often have a modular design, allowing print stations to be added or removed depending on the job’s requirements. This flexibility is beneficial for printers who work on a range of different projects.
5. Economical Footprint:
The vertical stacking of the print stations makes stack presses ideal for environments with limited floor space. Despite the vertical design, these systems can be compact enough to fit into smaller production spaces without sacrificing functionality.
Advantages of Stack Press Systems in Flexography
When choosing a press system for flexographic printing, the advantages offered by stack presses can be significant, especially for businesses focusing on packaging.
1. Space Efficiency
Unlike inline presses that stretch horizontally and take up considerable space, stack presses are more compact due to their vertical build. This makes them a perfect choice for operations where floor space is at a premium, allowing more room for other essential machinery or storage without compromising on the press’s effectiveness.
2. Enhanced Color Management
The ability to handle multiple colors is a crucial aspect of modern packaging design. Stack presses are designed to manage complex color schemes, including CMYK and spot colors, making them ideal for high-quality, detailed prints. With each color station independently adjustable, operators can ensure precise registration, resulting in vibrant, accurate colors on the final product.
3. Versatility in Substrates
From food packaging to flexible films and cardboard, stack presses excel at printing on a broad range of substrates. This versatility enables businesses to use one machine for a variety of product lines, reducing the need for multiple presses and minimizing operational costs.
4. Easy Maintenance and Operation
Since stack presses offer good accessibility to each color unit, operators can more easily carry out maintenance, such as cleaning, color changeovers, and roller replacements. This ease of use reduces downtime and increases overall efficiency in the production line.
5. Cost Efficiency in Long Runs
While stack presses may have a higher upfront cost than some alternatives, they are particularly efficient for long print runs. The ability to print multiple colors simultaneously in a single pass reduces labor and time, making the stack press an economical choice for high-volume jobs.
Common Applications of Stack Press Systems
Stack press systems are highly versatile and can be used for a wide variety of applications. Here are some common industries and products where stack presses are frequently employed:
1. Packaging Industry:
From food wrappers to beverage labels, the packaging industry relies heavily on stack presses to deliver consistent, high-quality prints. The ability to print on various substrates makes stack presses ideal for flexible packaging solutions.
2. Paper and Cardboard Products:
Whether it’s printing on cartons, boxes, or paper bags, stack presses provide the color accuracy and durability needed for these materials. The vertical design also makes handling thicker substrates easier without compromising on print quality.
3. Film and Plastic Applications:
Stack presses are often used for printing on films and plastics, especially in industries like healthcare, where flexible and durable packaging is essential. These presses ensure that even delicate substrates like shrink films are printed with precision.
4. Specialty Products:
Stack presses can also be used to print special editions or limited runs of packaging that require intricate designs or special inks. For instance, metallic or gloss finishes can be applied seamlessly using a stack press, providing a unique look that appeals to consumers.
How to Choose the Right Stack Press System
Investing in a stack press system can be a game-changer for your flexographic printing business, but choosing the right model requires careful consideration. Here are some factors to keep in mind:
1. Substrate Requirements
Make sure the stack press you choose is compatible with the types of substrates you work with most frequently. Whether it’s paper, plastic, or film, selecting a press that handles your materials effectively will ensure optimal results.
2. Number of Print Stations
If your business typically prints complex, multi-color designs, consider a stack press with more print stations. This will allow you to produce intricate designs in a single pass, reducing time and labor.
3. Space Constraints
Measure your available floor space to ensure that a vertical stack press will fit comfortably in your production area. Stack presses are often chosen for their space-saving design, but it’s still important to verify dimensions before making a purchase.
4. Budget
Stack press systems can vary widely in price, depending on features and capabilities. Consider the long-term return on investment by factoring in the efficiency, speed, and versatility of the press compared to its upfront cost.
5. Maintenance and Operator Skill Level
Evaluate the ease of maintenance and operation. Some stack presses are more user-friendly and require less manual intervention, while others may demand more skilled operators. Choose a press that aligns with your team’s capabilities and production goals.
Conclusion
Stack press systems represent a significant advancement in flexographic printing, providing unmatched versatility, efficiency, and precision. From their space-saving vertical design to their ability to handle complex, multi-color printing jobs, these systems have become a staple in the packaging and printing industries.
For companies looking to improve their production capabilities, investing in a stack press system could be the solution that unlocks new levels of productivity and print quality. By choosing the right stack press, businesses can not only meet the demands of today’s competitive marketplace but also position themselves for future growth in the ever-evolving world of flexographic printing.
FAQs
What are stack press systems used for in flexographic printing?
Stack press systems are primarily used for multi-color printing in the packaging industry, offering precision, flexibility, and efficiency in printing on various substrates like paper, film, and plastic.
How do stack press systems differ from central impression (CI) presses?
The main difference is the configuration. Stack presses use a vertical arrangement of print stations, while CI presses feature a central drum around which substrates are wrapped for printing. Stack presses are more compact and versatile in substrate handling.
Can stack press systems handle large print runs?
Yes, stack presses are ideal for long print runs due to their ability to print multiple colors in a single pass, reducing downtime and labor costs.
What substrates are compatible with stack press systems?
Stack presses can print on a wide range of substrates, including paper, plastic, film, cardboard, and flexible packaging materials.
Are stack press systems suitable for high-quality packaging printing?
Absolutely. Stack presses are designed for precision color registration and can produce vibrant, detailed prints, making them perfect for high-quality packaging.
What are the maintenance requirements for a stack press system?
Stack press systems are relatively easy to maintain, with accessible print stations for cleaning and color changes. Regular maintenance, such as roller cleaning and replacing worn components, ensures consistent performance.