This blog was written and submitted to us by Torben Wendland
During photopolymer washout processing in flexo platemaking, the final plate relief is revealed. Material which was polymerised in the processes before remains on the plate while unpolymerised material is removed.
Unlike in direct engraving, the material is not burned by a laser. Instead, two options are available for photopolymer washout processing in flexo platemaking:
- Dissolving and mechanical removal of the material (“solvent washout”) or
- Melting of the material to remove it (“thermal washout”)
In both ways it has to be ensured that the whole unpolymerised material is removed during the washout. For thermal washout, it is common that predefined washout settings are provided by the machine manufacturer or plate supplier. In solvent washout, the correct processing speed is determined through a washout test. The result is depending on the plate type, the machine and especially the washout solvent.
Solvent Washout
Solvent washout is the most common way of washout processing. The plate is rinsed with a solvent mixture containing different components to dissolve the different parts of the plate (polymer, LAMS, release layer etc.). Various kinds of solvents are available in the market. Following aspects are influenced by the choice of solvent or need to be considered when choosing a solvent:
- Washout speed
- Plate swelling
- Required drying time
- General plate quality (fine elements, plate surface etc.)
- Compatibility with the machine
During solvent washout, the plate is rinsed with the solvent while brushes are moving over the plate surface to take off unpolymerised material. The required washout speed or time is tested in advance: For this test, raw, unpolymerised plate pieces are washed out at different speeds to find the speed that generates the desired relief depth. Often plates are slightly over-washed to guarantee proper removal of the whole material. Once the washout step is finished the plate needs to be dried.
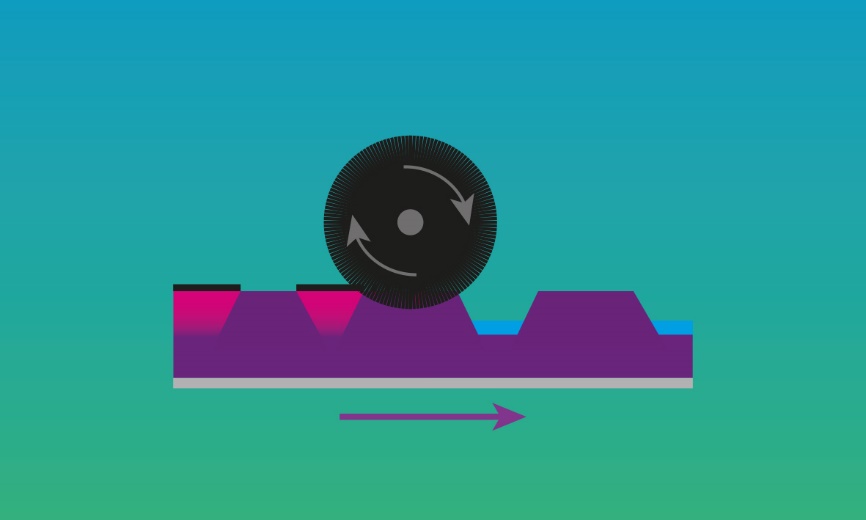
Thermal Washout
In thermal washout, this drying step is not required since no solvent is used. Instead, the polymer is heated up and brought in contact with a developer material. The liquified unpolymerised material keeps sticking to the developer material. Like this, layer by layer the unpolymerised material is removed from the plate. Several development passes are necessary to achieve the final relief depth. The deeper the desired relief, the more passes are usually necessary. After the thermal washout is finished, the plate is ready for post exposure and finishing.
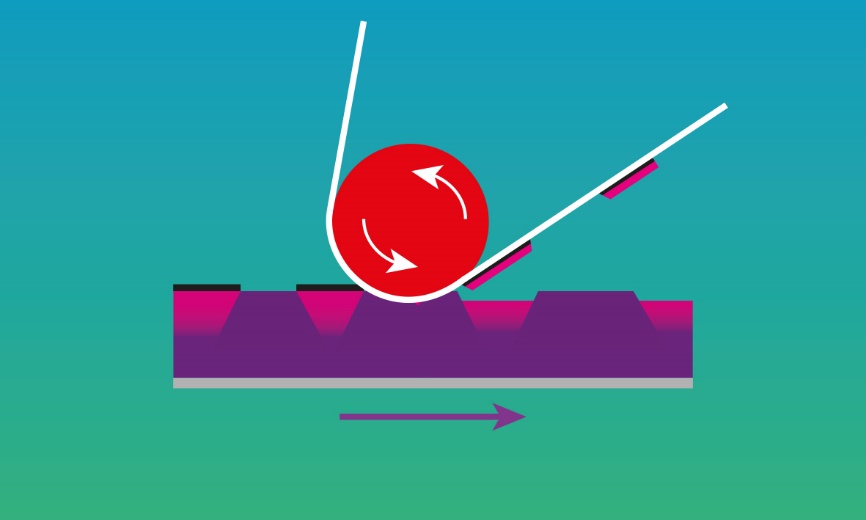