Dot gain is a prevalent occurrence in flexo printing and all printing processes. As dots transition from film to plate, they typically increase in size during exposure, especially in analogue plate processes. Subsequently, when an ink dot moves from the plate to the substrate, it can further expand as the ink spreads upon absorption.
How to Deal with Dot Gain?
A dot initially set at 50% on film may enlarge to 51% on the plate and eventually print on a flexographic press as a 65% or even larger dot. Factors such as the use of fluid ink and compressible plates in flexography play a role in increasing dot gain, with variations based on the press type and substrate characteristics.
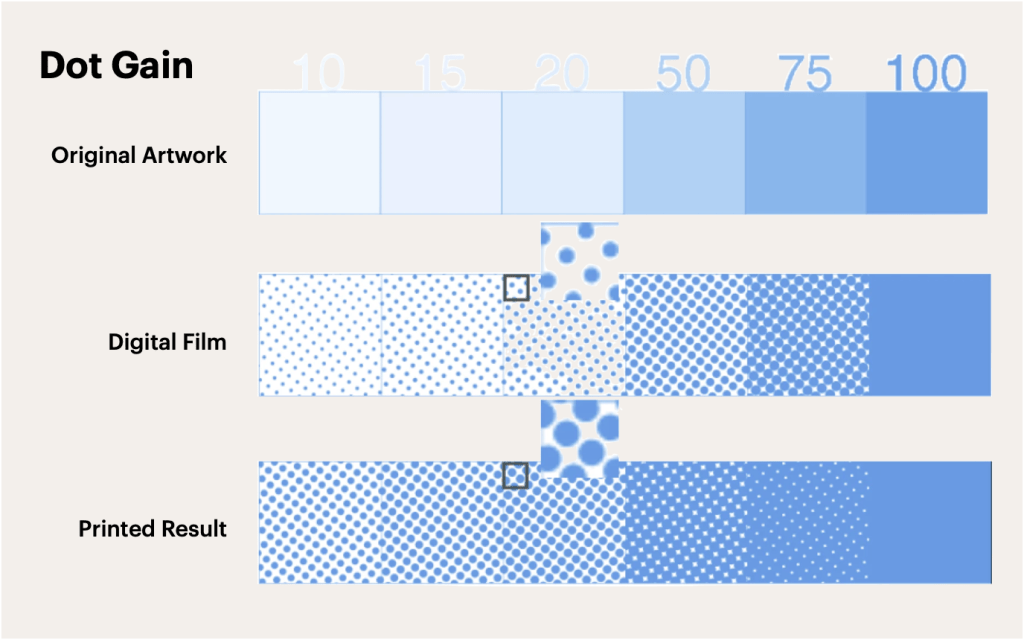
Notably, smooth non-absorbent films and coated papers experience lower levels of dot gain compared to absorbent or irregular surfaces like uncoated papers, newsprint, and corrugated liner board.
Despite its presence, dot gain is often consistent and foreseeable. Modern image and colour separation software can adjust dots based on input from the printer. Typically, printers conduct a fingerprinting analysis to provide dot gain data to colour separators or desktop designers. Adjustments to dots in colour separation films are made based on controlled target chart printing. Moreover, calibration features in raster image processors (RIPs), such as the Agfa Calibrator, are available to facilitate these adjustments.
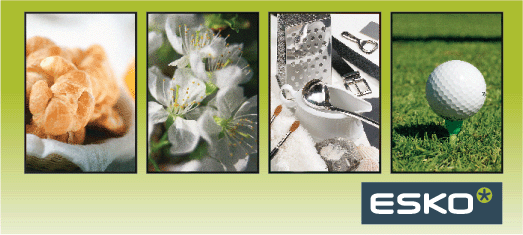
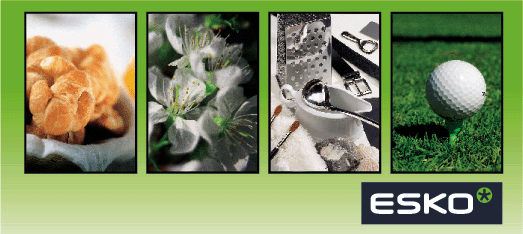
Factors to Consider
Impression Pressure
While ink transfer occurs under light pressure in the printing nip, the soft flexo plate undergoes slight deformation and compression during image transfer, leading to increased dot gain.
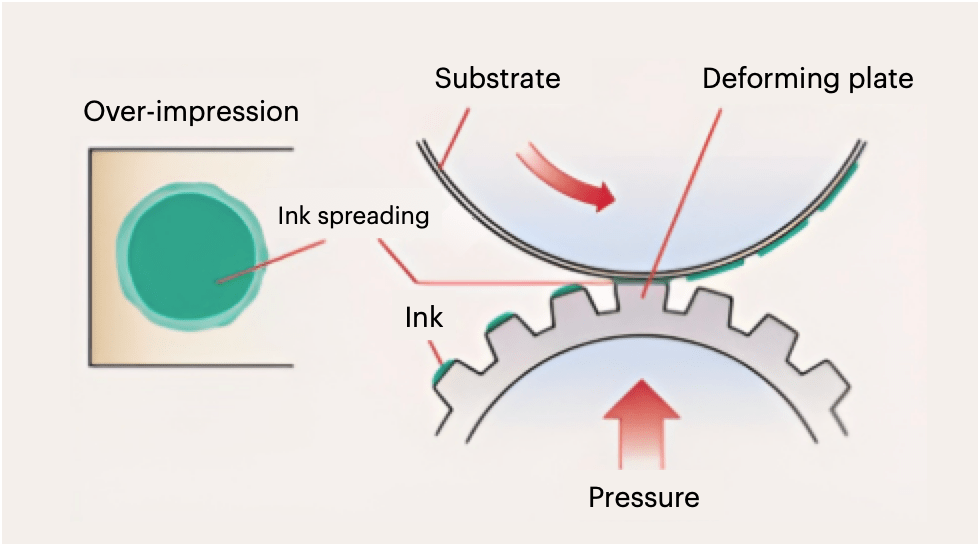
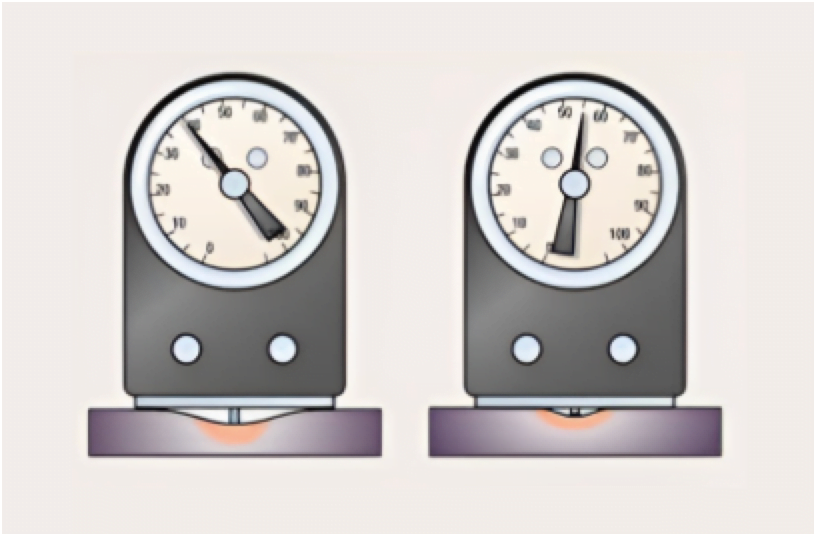
Plate Hardness
The hardness of plates affects dot gain levels. Harder plates compress less than softer ones, resulting in lower dot gain. To minimise dot gain, using a thin capped (0.002″~0.005″) surface layer with a higher hardness than the supporting plate material is recommended. Mounting the plate with compressible tape or a blanket that absorbs pressure can also help reduce dot gain.
Inks
Higher viscosity inks spread less quickly than lower viscosity inks. Low-viscosity flexographic inks tend to spread or flow out when transferred to the substrate before drying, contributing to dot gain.
In contrast, offset inks have a thicker consistency and are less prone to excessive spreading.
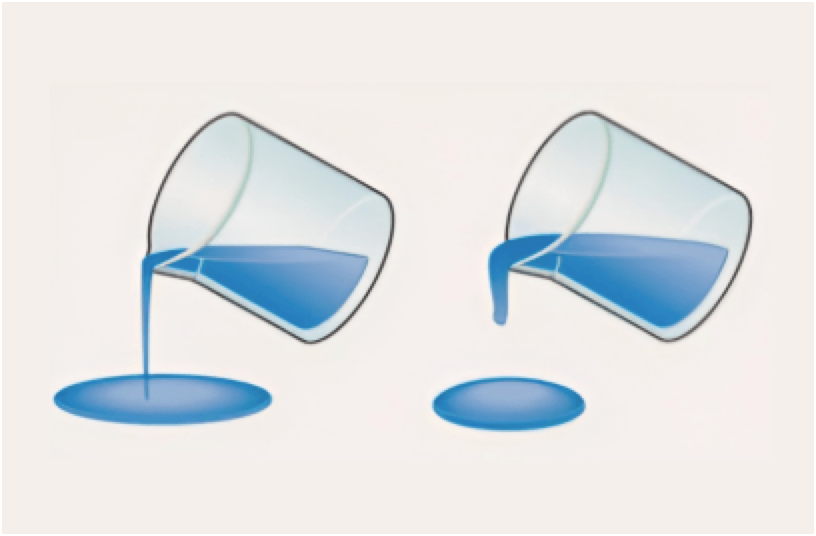
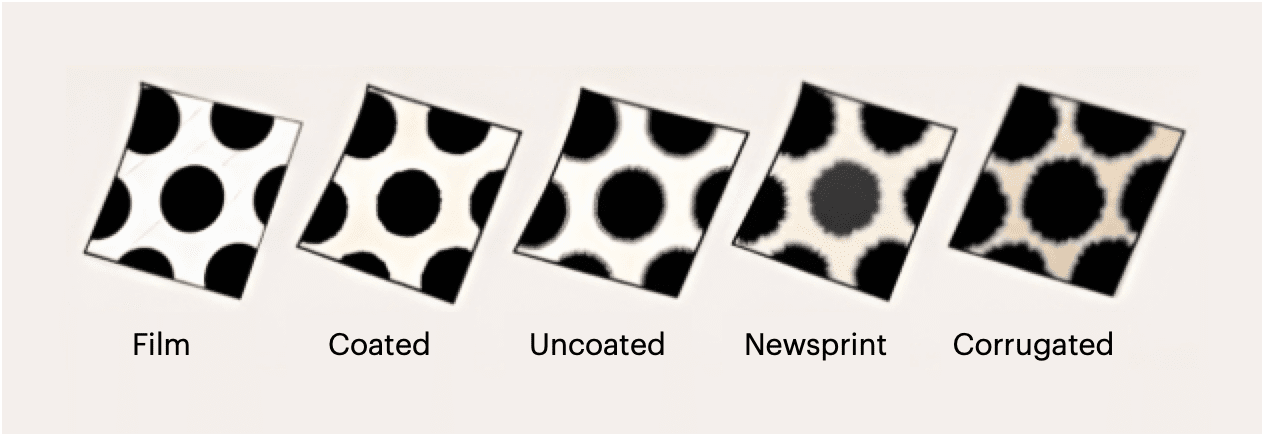
Substrates
The substrate’s surface or finish influences dot gain significantly. Smooth non-absorbent films and coated papers tend to maintain the dot shape well upon ink application, experiencing minimal spreading.
However, more absorbent and irregular surfaces, like uncoated paper, newsprint, and corrugated liner board, allow ink to spread beyond the intended dot shape and pattern due to the paper fibre acting as a wick and absorbing the ink.