This article is part of the FLEXO FLAW FIXING series
In the world of flexo printing, misregistration can be a frustrating obstacle to the seamless creation of high-quality prints. This misalignment of ink combinations on the substrate, even by the smallest of margins, can cause significant problems with print accuracy and overall quality. Identifying and eliminating the most common causes of misregistration is essential to maintaining the efficiency and productivity of the printing process. Let’s take a closer look at the main causes of misregistration and explore the corresponding remedies to effectively overcome these challenges.
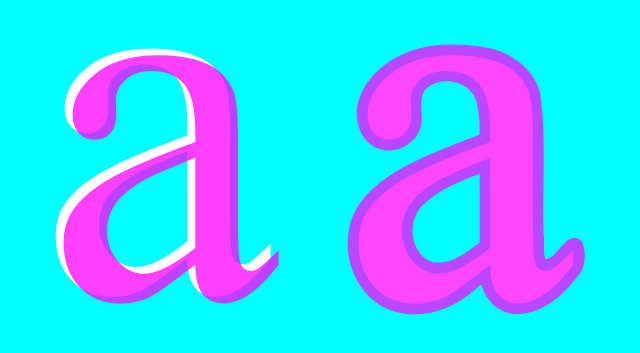
Causes of Misregistration and Remedies
Inaccurate Plate Mounting & Centring
- Use precision mounting equipment to ensure that the plates are in correct position.
- Double-check alignment with microdot or other registration marks before starting the print run.
Impression Cylinder Concentricity
- Regularly check and maintain cylinders with precision measuring tools, like dial indicators.
- If any deviations are found, the cylinder may need to be re-machined or replaced.
Cylinder, Plate and Sleeve Condition
- Implement a routine inspection protocol, clean regularly to prevent buildup, and repair or replace any damaged parts immediately.
Gear Condition
- Inspect gears for damage or wear and clean them of any debris that might cause misalignment.
- Check and maintain the tolerance levels of gear fits to avoid play that can lead to misregistration.
Idle Rollers Drag or Rotate Irregularly
- Maintain and lubricate rollers as appropriate and ensure that they’re free of any adhesives or substances causing drag.
Malfunctioning Web Guide
- Be aware of carrying out calibrations on the web guide system regularly.
- Confirm that the controller and sensor are functioning correctly and making appropriate adjustments in real time.
Web Growth or Fanning Out
- Recognise the normal expansion of materials and compensate accordingly with software or tension adjustments.
- Consider environmental factors in the press room, like humidity and temperature, which may affect substrate expansion.
Wandering Web
- Regularly calibrate tension control systems.
- Ensure edge guides are properly set up to mitigate lateral web movement.
Substrate Surface Tension
- Ensure the substrate is properly treated before printing to achieve an adequate surface energy, improving ink transfer.
- Adjust coronas or flame treaters as necessary if materials aren’t pre-treated.
Incorrect Tolerances
- Reinforce stringent pre-press protocols, ensuring all plates are of correct making.
- Adjust trapping dimensions and tolerances in the design stage to allow for any on-press variations.
Conclusion
In summary, managing misregistration in flexo is critical to maintaining print quality and efficiency. By understanding the various causes of misregistration, from plate mounting issues to gear alignment challenges, printers can take proactive steps to prevent misregistration. Regular maintenance, proper alignment procedures and careful inspection of press components are key aspects of ensuring smooth and accurate printing processes.
By implementing these measures and remaining vigilant to potential causes of misregistration, printers can minimise downtime, reduce waste and consistently deliver high quality prints. Taking a proactive approach to misregistration issues will not only improve print quality, but also streamline the printing process for greater overall efficiency.
This comprehensive approach to misregistration challenges will contribute to a smoother and more productive flexo printing operation, ultimately leading to improved results and greater customer satisfaction.