What are Anilox Rollers and Anilox Sleeves?
Anilox rollers and anilox sleeves are used in short inking units such as flexographic printing, and sometimes also in offset printing or print varnishing. They transfer the minimum necessary, constant amount of ink to the flexographic printing plate during the printing process.
What does the minimum amount of ink required mean?
It results from the roughness of the substrates. It also depends on the fineness or resolution of the elements to be printed. A closed ink film is required for transferring printing elements cleanly. It must cover the printing substrate’s surface. The finer the printing elements are, the less ink is needed. Less ink ensures even the finest elements are printed cleanly. With mixed printing forms, on the other hand, more ink is required. This is to ensure that even solid areas are printed homogeneously closed with the desired ink density.
What does the quantity of ink offered by an anilox roller depend on? The anilox roller engraving with the geometry of the cells or engraved structures is very important for this.

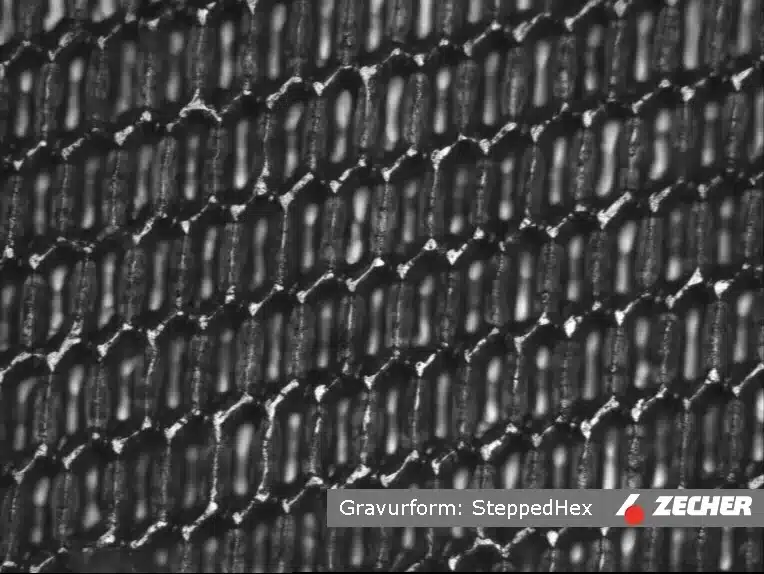
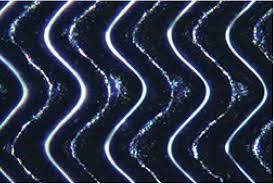
For high-quality halftone flexo printing, two other forms of engraving have recently emerged in addition to the established 60° hexagonal engraving of cells. One is the engraving of an extended cell shape at an angle of 60°, and the other is the engraving of lines in the form of an open channel structure.
What do these new engraving forms offer?
They are intended to Increase anilox roller resolution is for finer cliché screen ruling. It achieves this without losing any ink quantity offered. Finer plate screen rulings enable homogeneous ink transfer. This is due to extended cells or channel structure. Thus, the ink film transferred onto the substrate is more even and closed. The same volume specs sometimes lead to higher dot gain. So, it’s crucial to discuss anilox roller specs with the manufacturer. Another advantage of the new engraving forms lies in easier cleaning, thanks to the larger cell openings.
What fineness of the Anilox rollers and thus screen ruling is required?
The fineness of an anilox roller indicates how many screen cells there are on a distance of one centimetre. When printing on plastic films, in label printing and flexible packaging, a ratio of 1∶6.5 to 1∶7.5 is generally assumed for the plate screen ruling to the screen roller ruling.
In practice, this means that if a 1% tonal value is to be printed with a 60° plate screen, the anilox roller must have a fineness of at least 400 L/cm for the 60° hexagonal engraving form. Its scoop volume is then 4 cm³/cm² for non-absorbent substrates, for example. For engravings of the extended cell form and channel structures, this ratio can increase to 1∶9.5 in order to print a halftone value of the same specification, i.e. 500 to 580 L/cm. It is not possible to translate volume specifications from one supplier to another, as each anilox roll manufacturer uses different measuring methods.
In corrugated board printing, with its absorbent substrates, the ratio is more like 1∶5. If, for example, a 42 cliché screen ruling is to be printed, anilox rollers with a ruling of 225 L/cm are used for process inks. Here, too, the screen ruling increases with engravings of the extended cell form and channel structures and increases to 340 L/cm, which also increases the ratio, in this example to 1∶8.