This blog was written and submitted to us by Torben Wendland
The drying step in flexo platemaking of photopolymer plates is only necessary for solvent processed plates. Thermally processed plates do not require this step, since no solvent needs to be evaporated from the plate.
For solvent processed plates, the drying step is used to remove the solvent that has migrated into the plate during plate washout. Plates are usually dried in a dedicated drying unit which is running at a temperature of 50-60°C. The time the plate has to remain in the dryer is depending on various factors like:
- Plate type and thickness
- Relief depth and washout speed
- Solvent type
- Dryer technology
Tips on Drying Time
Plate suppliers are giving recommendations for the drying time of their specific plate types processed under standard conditions. Usually, thicker plates with a deeper relief require slower washout speeds. The slower the washout speed, the longer the contact time with the solvent which increases the required drying time. Typical drying times are ranging in between 1 hour (for thin plates) and 4 hours (for the thickest plates).
Therefore, the drying step is the one step in the whole solvent platemaking process that takes the most time. In the direct comparison with thermal platemaking, plate drying is the main reason for the time saving of the thermal process.
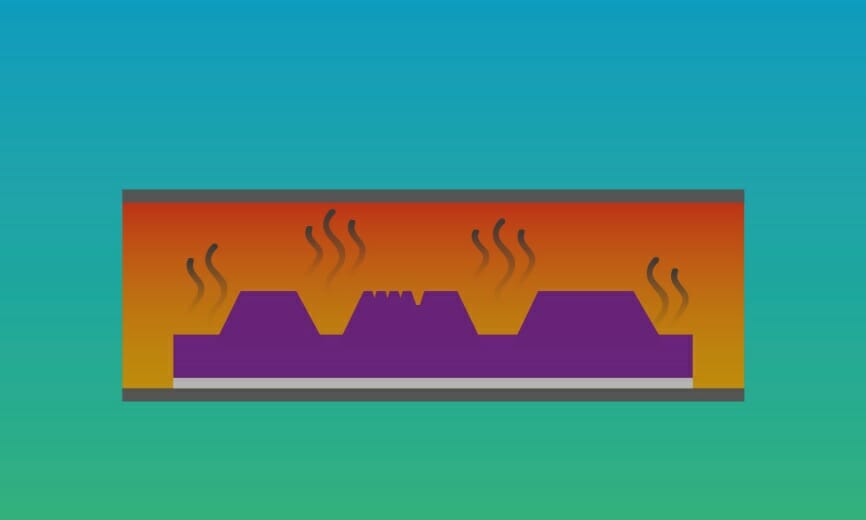
To determine the required drying time, the plate thickness can be measured in certain time intervals. The plate swells during plate washout as solvent migrates into the plate. A sufficient drying time is achieved, when the plate is dried back evenly to its intended thickness.
Other Points to Consider
Besides the correct temperature in the drying unit, an even air distribution and sufficient air exchange is required to dry the plates evenly. Plates are put into the dryer either manually by the operator after the washout process or automatically through an Inline system.
After the drying step is completed, the plates should be stored at room temperature for some time to let the plate cool down. This procedure is important especially to prevent registration problems between different plate separations. After the plates have rested and accommodated to room temperature, they are ready for post exposure and plate finishing – the last processing step.