Flexographic Printing and Its Components
Flexography, commonly known as flexo printing, is a variant of relief printing. It uses a flexible, compressible plate to transfer ink to a substrate. Unlike other printing methods, the image areas on the plate are raised above the non-image areas, allowing for precise ink application. The purpose of this article is to provide a comprehensive overview of flexography for your basic understanding.
In this article, we are going to introduce the basic components and principles of flexo printing. The special inking system set flexography apart from other printing techniques. An anilox roll, which is an ink metering cylinder, applies ink to these raised areas. The plate then makes light contact with the substrate to transfer the image. This minimal pressure is advantageous when printing on delicate materials. Corrugated board, for example, is susceptible to damage from excessive pressure in other printing processes.
Inking System
Flexographic printing units contain various inking systems designed to meet different printing requirements. The main types are:
- Two-roll Unit with One Doctor Blade: Typically found on older flexographic presses and narrow web presses. In this setup, the rubber-coated fountain roller rotates in an ink bath, drawing ink onto the anilox roll. The doctor blade scrapes excess ink from the non-cellular areas of the screen roll. This design ensures that only a measured amount of ink contacts the plate.
- Dual Doctor Ink Chamber System: More common on modern wide web presses, this system eliminates the need for a dampening roller and ink pan. Ink is delivered directly to the anilox roll through an enclosed chamber. This setup allows for a more precise and clean ink delivery process, resulting in higher quality prints.
Anilox Rolls
The anilox roll is critical to controlling the amount of ink transferred to the plate. It has a surface engraved with microscopic cells that are responsible for ink metering. The following characteristics of anilox rollers are essential:
- Cells Per Inch (CPI): Cells per inch range from 140 to 1200 CPI. Higher cell counts deliver less ink, which is beneficial for high-resolution printing.
- Cell Volume (BCM): This measures the amount of ink a cell can hold, with volumes ranging from 1.8 to 17 billion cubic microns per square inch. As the number of cells increases, the cell volume tends to decrease.
- Cell Angle: Standard cell angles are 30°, 45° and 60°. A 60° angle is favourable because it provides better ink transfer and reduces the risk of moiré patterns that can occur when the screen angles of the plate and anilox roll are misaligned.
Application | Substrate | Cells Per Inch | Cell Volume |
line art | corrugated board | 200-280 | 7-8.5 BCM |
halftones at 65 lpi | corrugated board | 360-400 | 4.0-5.5 BCM |
4/c halftones at 133 lpi | polyethylene bags | 600-900 | 1.8-2.0 BCM |
Flexographic Printing Presses
Flexographic presses are categorised into two main configurations, each suitable for different printing needs:
- Central Impression (CI) Press: Also known as a Common Impression Cylinder (CIC) press, this configuration typically has 4 to 8 colour units with its limitation to single-sided printing. It excels in high-speed printing with precise registration, especially on stretchable films, but requires longer makeready times due to more complex unit access.
- In-line Press: This type can accommodate up to 12 colour units and provides two-sided printing with a turner bar. It is ideal for thick substrates such as paperboard and is often in conjunction with other converting operations such as laminating, rotary die-cutting, and side-seal bag converting. However, it’s less suitable for printing thin packaging films.
- Stack Press: Capable of accommodating from 1 to 8 colour units, some stack presses offer the ability to print on both sides. When working with thin films, it is critical to maintain traps (overlapping colours) of no less than 1/64″ to ensure quality results. Industry often integrates these presses into in-line setups alongside other converting operations such as laminating, rotary and flatbed die-cutting, and side-seal bag converting.
- Corrugated Press: Similar in configuration to an in-line press, this sheet-fed option can handle widths up to 120 inches and typically supports up to 4 colour units. Designed primarily for single-sided printing, it offers less precise registration capabilities than other presses.
Flexographic Printing Plates
Flexographic printing uses two main types of plates, each with unique characteristics:
- Photopolymer Plates: These plates are made of light-sensitive photopolymer, either in solid sheets or in a liquid state. By exposing a plate through a film negative, the image area rises after the removal of the non-image area after exposure. Liquid photopolymer solidifies when exposed to ultraviolet light, forming the raised image areas on the plate.
- Laser Ablated Plates: This advanced technology allows for direct-to-plate imaging, eliminating the need for film negatives. A laser etches the image directly onto the photopolymer plate, which then undergoes other conventional processes. These plates can achieve seamless repeats and continuous background colours, which are particularly useful for certain design requirements.
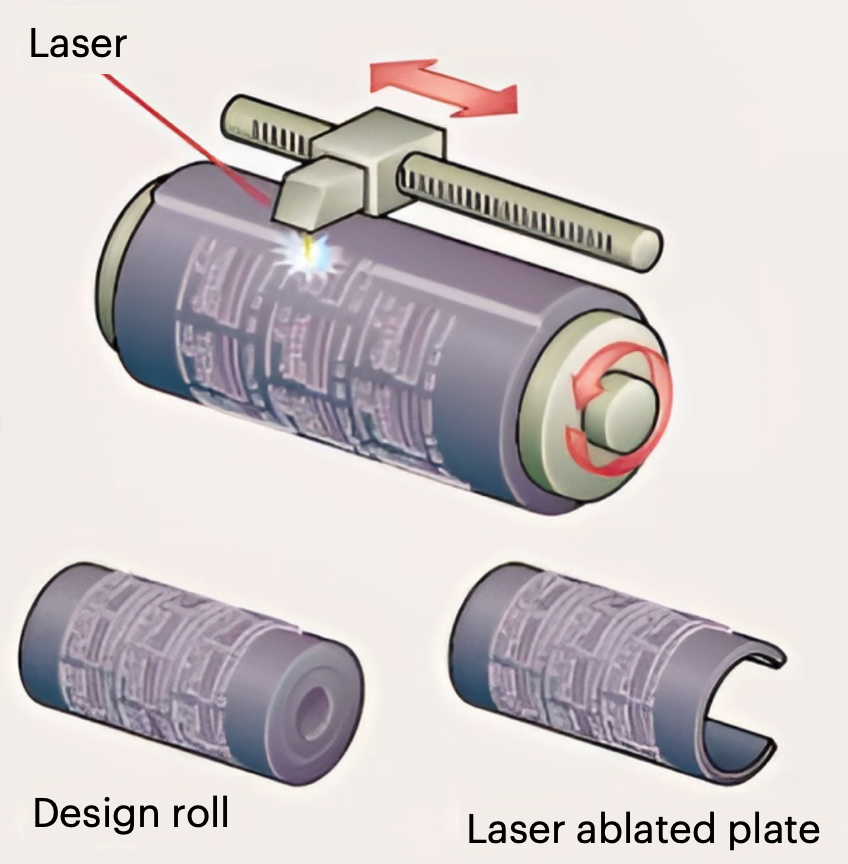
Recap
Flexography is a versatile, efficient printing process that is well suited to a wide range of substrates, from flexible films to corrugated boards. This comprehensive overview of flexography has introduced core components such as inking systems, anilox rolls, press types, and plates, each of which plays a critical role in achieving high-quality prints.
Understanding these elements allows printers to optimise their operations and meet specific customer needs. Continued advancements in flexo technology ensure its continued relevance in the modern printing landscape. We hope this article has provided you with a comprehensive overview of the intricate technique of flexography.