Halftone and screening in flexo is a special printing technique. Let’s understand it better.
Throughout its history, flexography has been printing quality line art and spot colours on a wide variety of substrates. However, it is the recently improved capability of high-quality, economical four-colour process printing that has given flexography an edge over other processes for packaging applications. Let’s have a look at some illustrations of halftones and screening in flexo.
Halftone
In flexography, the shape of the halftone dot used to reproduce a continuous tone image can significantly affect the density of the image. Halftone dots can be generated in a number of shapes, including square, elliptical, octagonal, and both symmetrical and asymmetrical dots.
Dot Shapes and the Respective Coverages
At 50% coverage, for example, square dots produce a pattern resembling a checkerboard, with individual dots just beginning to join at their corners.
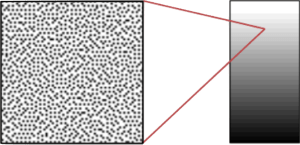
Screen Tints and Gradations
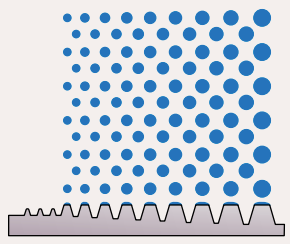
Highlight
Most photopolymer plates are capable of holding a 2% highlight dot. If plates aren’t properly exposed, however, screen tints and highlight dots less than 3% tend to drop out. Because the small dots of highlight areas are subject to relatively large dot gain, it is important that any highlight limitations are discussed with the printer before separations are made. Although printers in offset lithography can print acceptable highlights using 5% film dots, flexographic printers may have to reduce a similarly bright highlight to 2%, taking into account the additions of dot gain.
Gradations and Vignettes
Flexographic dot gain on highlights makes it difficult to print a fade-to-white gradation without a harsh break at the highlight edge. When designing images for flexography, it is best to fade off the end of the design (rather than to white). Or you can also place a border at the highlight end of a vignette.
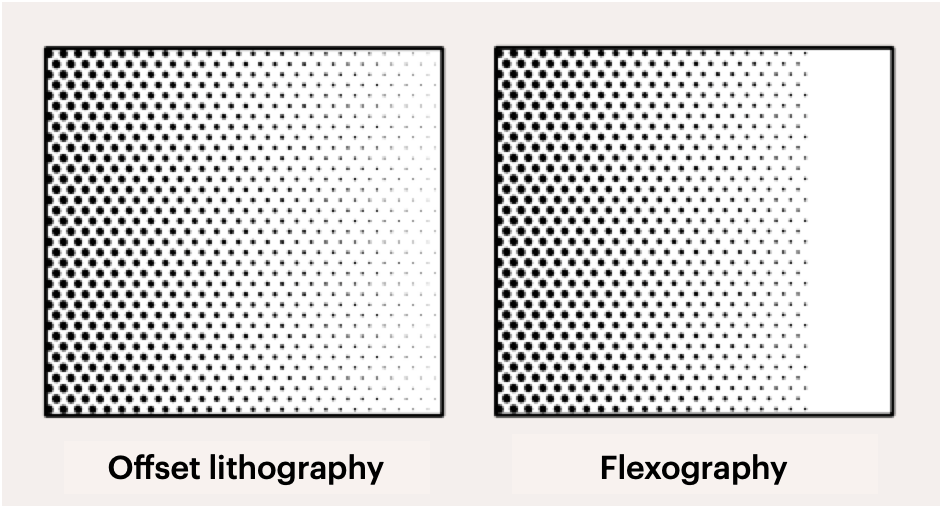
Density Jump
When plates are created from film, dot gain increases the joining of the dots. This causes sudden jumps in density in the printed image, rather than a smooth, continuous transition.
To minimise the density jumps, printers can use other kinds of dots that remain discreet and retain their shape, even at coverages of sixty and seventy percent. A round dot, or octagonal dot are often used. Though most design software can specify round dots, selection of dot shape should occur early in the process to avoid choosing a shape not available in the RIP, imagesetter, or platesetter.
Screening
Screen Ruling and Application
Selection of proper screen ruling, which is critical to four-colour process flexography, is often dictated by the type of substrate. Anilox cell count and screen ruling for separations should be correlated for best results. The cells of the anilox, which ink a halftone plate, should be large enough to produce appropriate colour strength. However it should not be so large that the halftone dots will dip into them like an inkwell. For conventional halftones, resolution is expressed as the number of lines of halftone dots per inch, also called screen ruling or LPI. Higher screen rulings produce higher resolution images because there are more dots per square inch used to reproduce detail. Compare the images in a newspaper (low screen ruling) to a picture in a monthly magazine (high screen ruling).
Lines per Inch (LPI)__________Cells per Inch (CPI)__________Application
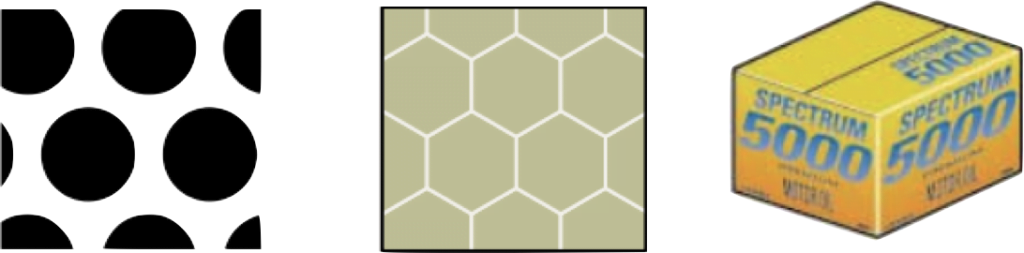
The corrugated industry prints halftones screened at 45, 55, 65, or 85 LPI
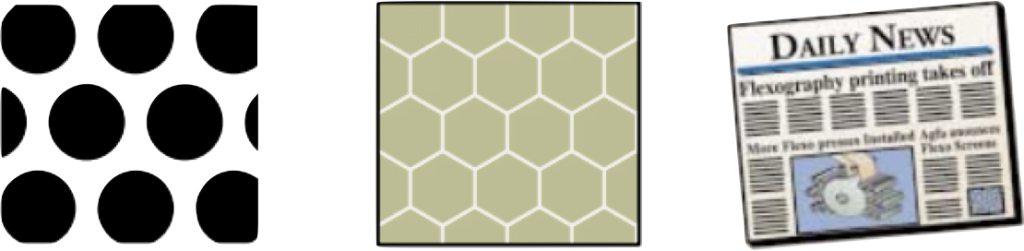
Flexographic newspaper presses print halftones screened between 65 and 100 LPI
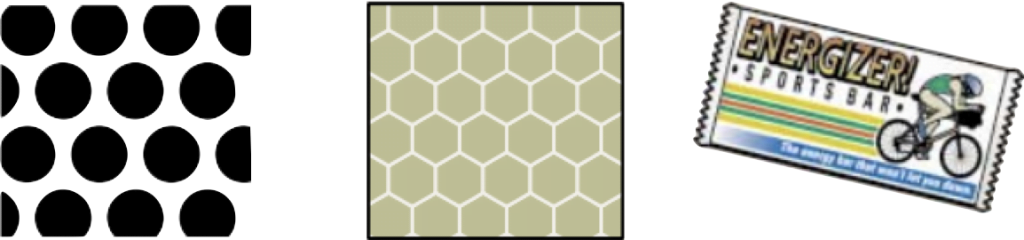
Flexible packaging on film substrates is commonly done at 120 and 150 LPI
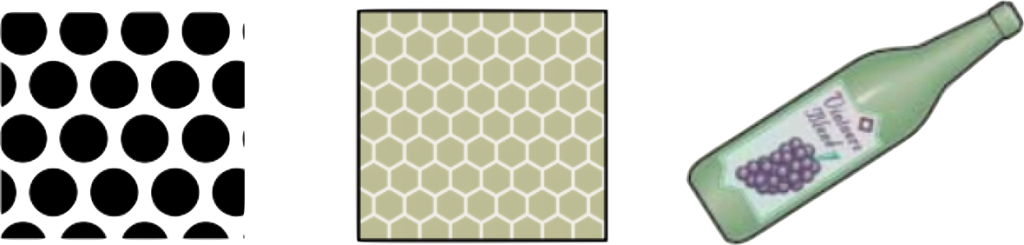
High quality label presses have the capability of printing 200-LPI images
Stochastic Screening
Stochastic, or frequency modulated (FM) screening, can offer advantages over conventional halftone screening. This screening technique eliminates the possibility of moiré. It also allows the flexographic printer to use HiFi colour, which involves the application of six or seven process colours. Dot size used for stochastic screening, however, is extremely small, comparable in size to the highlight dot of conventional screening. Since flexography is subject to significant dot gain, stochastic screening should only be used after the printer and colour separator have performed press fingerprints to determine the ideal dot size and accurate compensation for dot gain.