In the diverse world of printing, the question of how flexo presses transfer images onto substrates opens up a discussion on the pivotal role of the flexo inking unit. Flexographic printing, renowned for its adaptability across various substrates and efficient production speeds, relies heavily on its inking systems to achieve high-quality prints. Among these, the ink metering roll, chambered doctor blade system, and central impression drum stand out as fundamental components. This article delves into how each system functions, offering insights to businesses on selecting the most suitable one for their operations.
Ink Metering Roll in flexo inking unit
The ink metering roll, often found in simpler and older flexo presses, plays a critical part in transferring ink to the printing plate. It works by spinning in an ink pan, picking up ink, and transferring it through a series of rolls until it reaches the printing plate. The key to this system is the fine adjustment available on the doctor blade and metering roll, allowing for precise control over the amount of ink applied to the plate. This control is crucial for maintaining print quality, especially in runs where ink consistency can significantly affect the final product’s appearance.
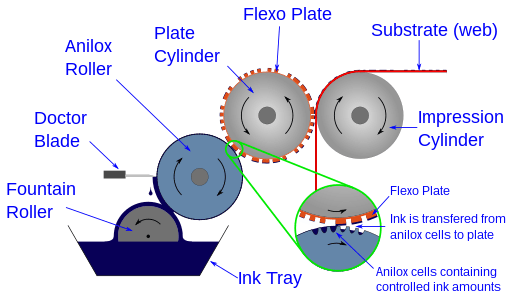
The suitability of an ink metering roll system largely depends on the print job’s complexity and the desired level of precision. It tends to be more appropriate for straightforward jobs with fewer intricacies and where high-speed production is less of a priority. This simplicity and ease of operation make it a cost-effective solution for businesses focusing on uncomplicated designs and those just beginning in the flexographic printing sector.
Chambered Doctor Blade System in flexo inking unit
A more advanced and widely adopted system is the chambered doctor blade. This setup revolutionises ink application by enclosing the ink within a chamber, tightly sealed against the anilox roll with a doctor blade on each side. One blade wipes excess ink from the anilox roll’s surface, ensuring that only the ink within the engraved cells is transferred to the plate, while the other blade keeps the chamber replenished with ink.
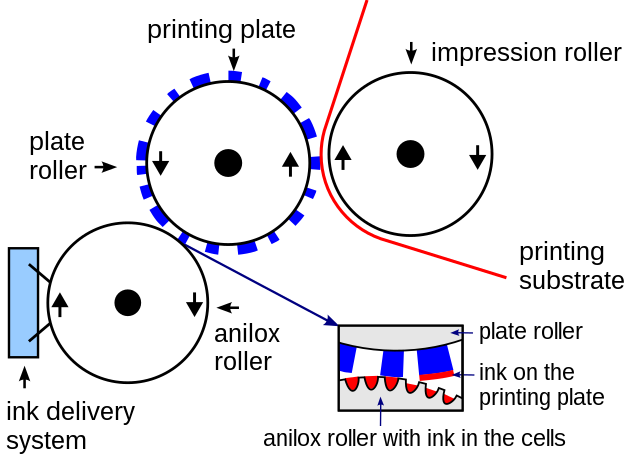
This system excels by offering exceptional control over ink film thickness, leading to higher-quality prints and reduced ink consumption. The chambered doctor blade is particularly favourable for jobs requiring intricate details, gradients, and high-quality finishes across a range of substrates. Moreover, its efficiency in ink use and the ability to swiftly change colours make it an ideal choice for businesses aiming for high-quality output and operational flexibility.
Central Impression Drum in flexo inking unit
The central impression (CI) drum system takes a different approach. It is designed around a large, central drum that holds the substrate in place while the print stations, each equipped with its inking system, move around it. This configuration is beneficial for printing on delicate substrates as it minimises tension and ensures precise registration, critical for high-quality multicolour prints.
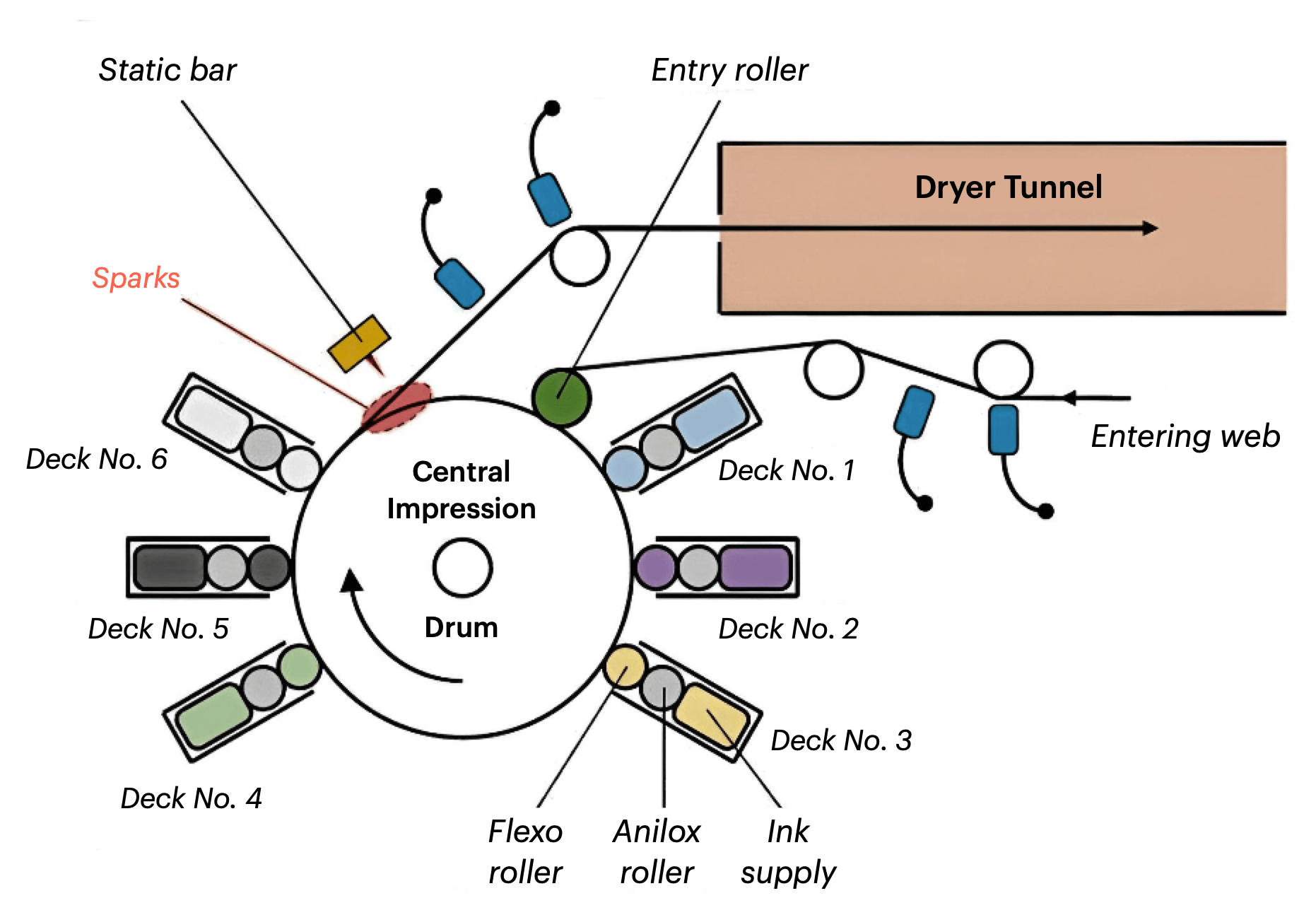
The CI drum’s ability to maintain substrate stability and achieve consistent tension control across the print process makes it especially suitable for businesses that specialise in high-end, multicolour work on a variety of substrates, including those that are lightweight or stretch-prone. While this system may require a larger initial investment, its potential for superior print quality and efficiency in long runs can offer a significant return on investment for firms engaged in producing premium packaging and labels.
Choosing the Right System for Your Business
Selecting the most suitable inking system hinges on several factors, including print job complexity, substrate variety, quality requirements, and production efficiency. For businesses focusing on simple designs and seeking an entry-level or cost-effective solution, the ink metering roll presents a viable option. It provides a straightforward setup that’s relatively easy to operate and maintain, ideal for smaller-scale operations or those with a limited variety of print jobs.
Conversely, the chambered doctor blade system represents a step up for businesses prioritising print quality and versatility. Its efficient ink use, coupled with its adaptability to different substrates and designs, makes it a sound investment for firms aiming for growth and diversity in their product offerings. This system is particularly useful for those engaged in producing detailed, high-quality prints across a range of materials.
Lastly, the central impression drum system is best suited for businesses at the forefront of the flexographic printing industry, undertaking complex, high-volume print runs on varied substrates. Its superior registration and substrate handling capabilities ensure top-notch print quality, making it an ideal choice for premium packaging and label production.
In conclusion, understanding the intricacies of each inking system and assessing how they align with your business’s specific needs is fundamental to making an informed decision. Whether it’s the simplicity of the ink metering roll, the precision of the chambered doctor blade system, or the superiority of the central impression drum, the right choice will pave the way for enhanced print quality, efficiency, and ultimately, business success.