What is the general purpose of mounting tapes for flexo printing?
Well – it needs to stick! Flexographic printing requires mounting tapes to fixate the printing plate on either a printing cylinder or a printing sleeve. In simple terms, the mounting tape for flexo printing is the bond between two key elements.
Mounting Tapes for Flexo Printing: Present and Past
The design of the mounting tape, which is always coated with an adhesive on both sides, has changed over the decades and from a pure connector between plate and roll, the mounting tape has been upgraded with foam materials to improve the print characteristics and the performance in the printing press.
Mounting Tapes Used-to-Be
In the early stages, printing plates for pretty much all of the flexible packaging and label applications have been rather thick with 2.84 mm. The plate was flexible and soft enough to absorb some of the irregularities of the substrate and likewise some of the vibrations causes by plate bounce or the machine itself.
This printing plate thickness however had a lot of limitation in terms of screen count or fine line reproduction. The double adhesive mounting tapes used where mainly 0.20 mm in thickness and mounted to the steel cylinder and the PET backside of the printing plate. The purpose – hold the plate properly in place and position while printing.
Evolving over Time
Well, then, many different evolutions happened. Flexo printing plates became thinner and harder to allow better resolutions and finer lines. At one point there was a trend to use 0.76 mm photopolymer plates which allowed to reproduce very small dots, but the handling was very difficult, which made the 1.14 mm plate and the 1.70 mm the more common one. Since the plate was no longer flexible enough to absorb tolerances in press caused by substrates or the different printing press parts, the mounting tape now had this role to play.
The mounting tape became compressible with a a thin foam layer in between the two adhesive layers and the carrier foil. The tape now became an even more essential part to the printing process. No longer just holding the flexo plate in place, but also improving the print quality due to its cushion layer. Since the cushion required some space, tapes became also thicker. Now there were thicknesses of 0.38 mm, 0.50 mm and 0.55 mm.
The names for these tapes also evolved from plate mounting tapes, to double adhesive cushion tapes, sticky back, foam tapes, you name it.
Other Requirements to Fulfil
What else does a flexo tape need to do? Ideally it holds the plate in position. But it also needs to be removed in from the plate later on without destroying the plate and without leaving residue. Further, it needs to stick to different surfaces such as steel cylinders and sleeves with different surfaces. Again, it needs to be removed from the surfaces without leaving adhesive behind. Additionally, flexo printing presses operate in different environments, with high and low humidity or temperature. Presses can have long runs or short runs and cylinders may be small or large in diameter.
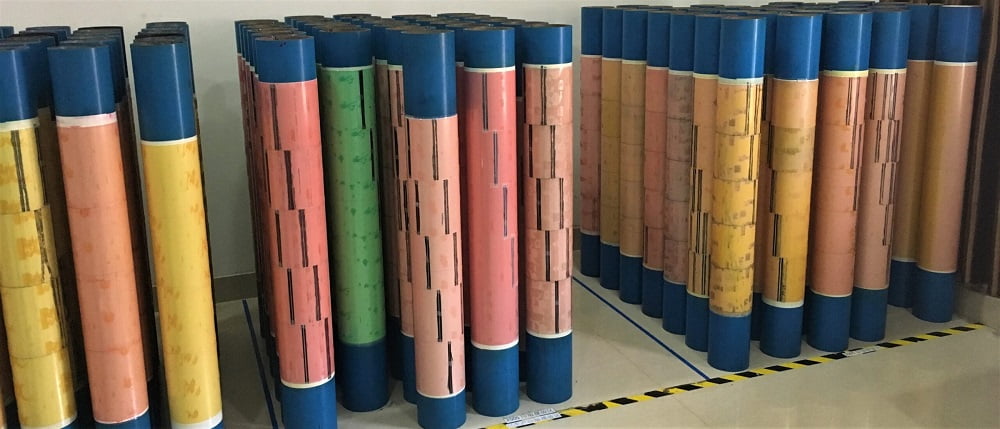
What sounds simple involves a lot of knowledge and technology about adhesive systems, foam materials and print characteristic. There are several manufactures who have that knowledge which gives the printer the choice to find the ideal product for the need.