This blog was written and submitted to us by Sandra Kaiser. Visit Flexo Consulting to know more.
As with other printing processes, there are typical features by which flexographic printing identification can be done – for example, the crimped edges of fonts or line elements, uneven inking of the substrate, or the so-called flexo rosettes.
Never heard of typical flexographic printing identification features?These terms are easy to explain:
Squeeze margins are generally known features of letter press processes, and flexographic printing is one of them. The fonts are not composed of halftone dots as in gravure printing, for example – where they are recognisable as a sawtooth effect – but of line elements. These line elements can have squeeze margins, which can sometimes even be felt as a slight relief.
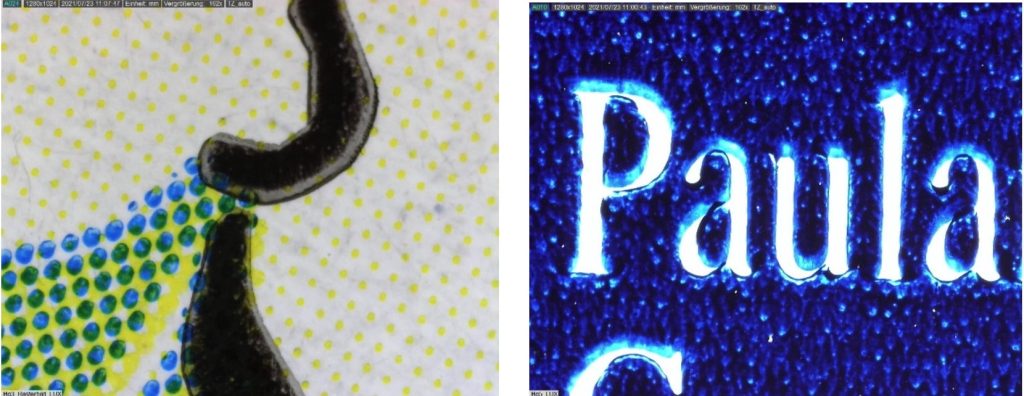
Here in the print example, a positive stroke element is shown on the left and a negative font on the right (both enlarged 162 times), each with a concise squeeze edge.
But how do these squeeze edges occur? There are several reasons for this: Squeeze marks can be caused by too much pressure or by the printing plate being too close to the substrate, and thickness tolerances in the printing plate can also be responsible. Either the printing plate or the substructure are too high or the wrong printing plate/substructure combination has been selected, for example the plate is too soft and the substructure too hard. Furthermore, the concentricity tolerance of the format cylinder may be too high.
However, if the clearance between the impression cylinder and the impression cylinder is too small, there is a risk that bubbles will form between the printing form and the substrate. These can lead to uneven printing or even to defects. A printed area can appear cloudy or pebbly as a result of incorrect printing supply.
In order to achieve more uniform wetting/ inking of the substrate, surface technologies can provide a remedy during printing plate manufacture. The printing plate surface is laser-imaged in the form of microstructures. As a result, the ink is absorbed more evenly and transferred to the substrate. The result is clean ink laydown and, at the same time, the “washboard effect” in direct corrugated printing is minimised.
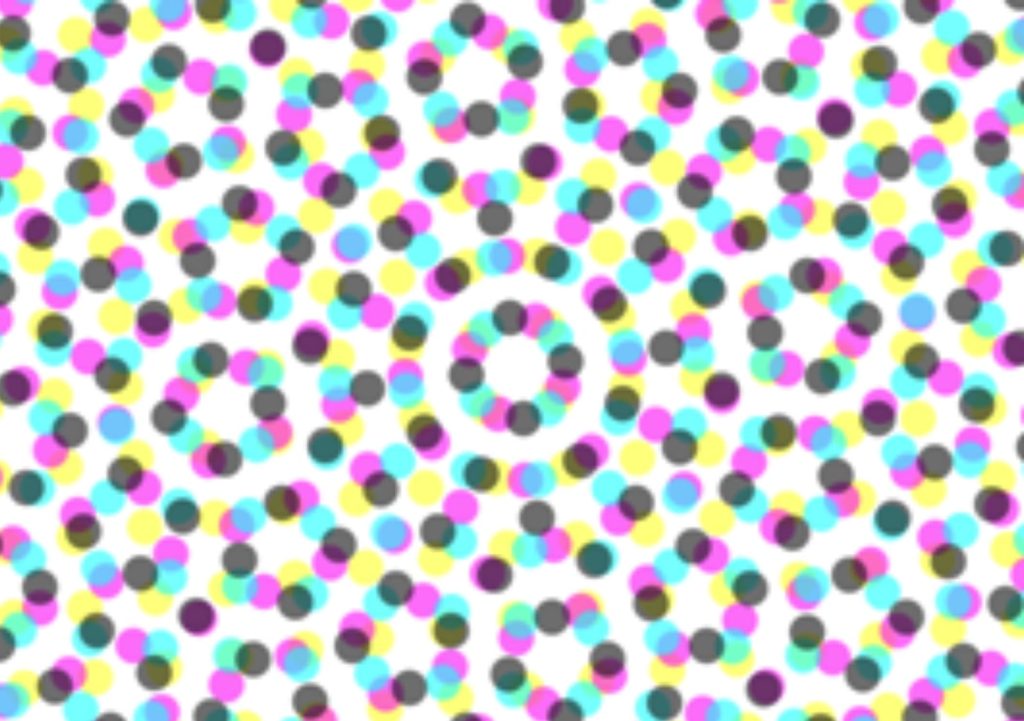
The last distinguishing feature of flexographic printing is the flexo rosette (see Fig. 2). It is created in halftone printing by the angulation of the colours cyan, magenta, yellow and black. A circular arrangement of the halftone dots is formed in the ink set, which becomes visible on closer inspection with a magnifier.