This blog was written and submitted to us by Torben Wendland
During laser imaging in flexo platemaking, the printing design is transferred from the file to the plate. The image is not yet polymerised, but is only existent as a mask.
Unlike conventional plates or other technologies that use film for image transfer, digital photopolymer plates are containing an embedded mask layer. This black mask or LAMS (Laser Ablative Mask System) is able to block the UV light during the main exposure. Laser imagers are used to selectively remove this black mask with the help of an IR laser. Common in the market are for example fibre lasers at 1064 nm or diode lasers at 940 nm wavelength.
Which imaging parameters need to be set up?
Important to consider before imaging is a correct setup of the focus depth and the imaging energy. This guarantees a sharp and linear image transfer from file to LAMS. Especially the imaging energy is a parameter that differs between brands or plate types and needs to be adjusted accordingly. The focus depth should at least be checked on a regular basis.
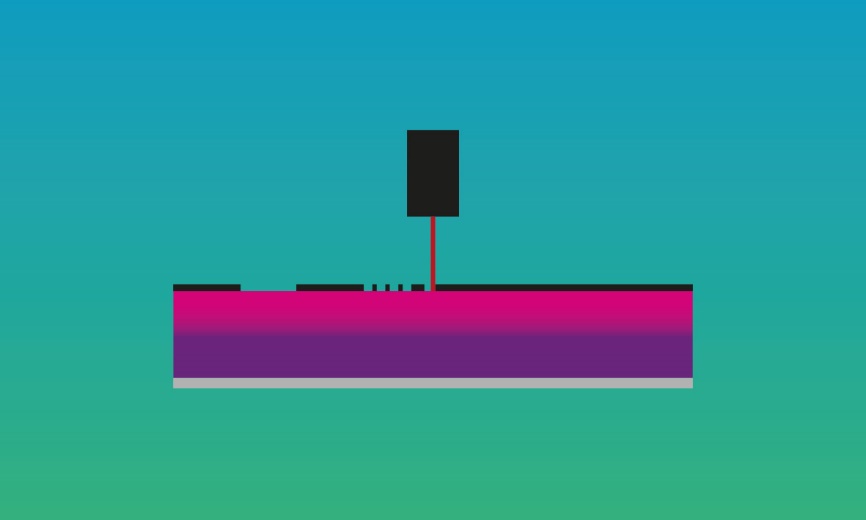
Which steps to perform during laser imaging of a flexo plate?
Prepress prepares the image for transfer to the plate, providing it as either a 1 Bit *.tiff or *.len file. Each colour separation of the job requires an individual file. You can place multiple files on a single photopolymer sheet, depending on the size of the image and of the raw plate.
Once you assemble the files on the sheet, you should select the plate type and thickness and send the job to the imager. You remove the cover sheet, mount the plate onto the imaging drum, and start the imaging process. In some cases, you may use indrum systems. After imaging, you demount the plate, and it’s ready for the main exposure.
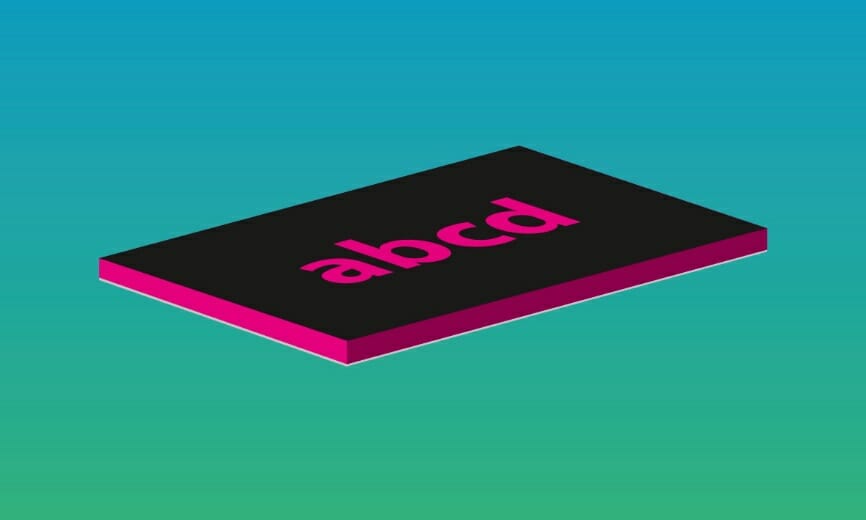
Which imaging resolutions to use?
Plate imagers are working with different file resolutions. Typical standard file resolutions are 2540 dpi or 2400 dpi. Higher demands in terms of fine details for example in security printing may require resolutions up to 10.000 dpi or higher. Also, special screening technologies like hybrid screenings for the highlights or surface screenings for the solids can be tailored to a certain file resolution. Resolution as well as the required imaging energy are influencing the length of the imaging process.