Flexo colour proofing stage, a crucial phase in the pre-press process, offers customers a visual preview of their final printed piece, guiding contractual agreements. Utilising press characterisation data, the proofing system constructs a colour profile vital for aligning incoming files with the anticipated printed output, ensuring an accurate representation.
In today’s landscape, inkjet devices are popular for creating final proofs, necessitating adjustments to the original ink sets to cater to ink hue variations, grey balances, dot gain considerations, and overprints mirroring press conditions. File formats for proofs should ideally support accurate inkjet reproduction, with raster proofs in 1-bit *.tiff or Len formats preferred for showcasing the dot structure’s influence on the final print’s visual impact.
The proofing process extends to faithfully replicating design elements like rosettes, trapping effects, and spot colours, with modern ink sets enhancing spot colour accuracy across a wide spectrum. Innovations in inkjet technology enable proofing on diverse substrates such as film and metallic media, even incorporating white ink for a more authentic representation of the final print. Including a control strip in each proof facilitates quality monitoring and maintenance.
What to Heed in Colour Proofing?
Proofing for halftone accuracy and colour matching in flexo can be intricate. Proofing method used in offset lithography may not be suitable for flexography due to the variation in substrates, spot colours, and flexo dot gain. Accurate proofing often necessitates using multiple methods.
- Substrates: Proofing methods are constrained by specific substrates, impacting ink colours due to substrate absorption and colour properties.
- Spot Colours: Matching spot colours accurately poses challenges for film-based and digital proofing methods designed for CMYK colours. Some printers offer a range of consistently reproducible spot colours for critical jobs, possibly using colour catalogues akin to Pantone® or FocolTone®.
- Dot Gain: Proofing systems, tailored for offset lithography dot gain, may not readily adjust for flexo dot gain. Establishing a profile for a given press using a colour management system allows digital proofing systems to simulate flexo dot gain accurately.
How to Proof the Colours in an Artwork?
Proofing for flexographic printing consists of several ways, which apply to different phases respectively.
Soft Proof
Initial design proofing often starts with a soft proof on a monitor, providing an overall design view. Proper calibration and CMS usage enhance colour fidelity, even though RGB colours on monitors may differ from CMYK or spot colours on print.
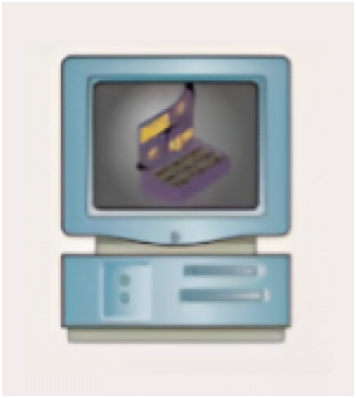
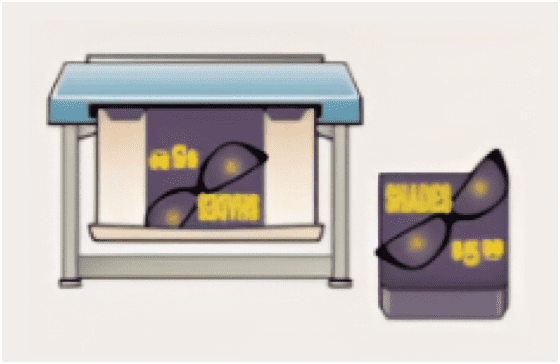
Digital Print Proof
Flexo printers utilise digital print proofs, incorporating high-end methods meeting industry standards. While CMYK-based, digital systems can offer accurate contract proofs when integrated with a colour management system.
Film Proofs
Film-based proofing systems cater to offset lithography’s dot gain compensation but require adjustments for flexo applications using two sets of films—one reducing and another increasing dots—for platemaking and proofing, respectively.
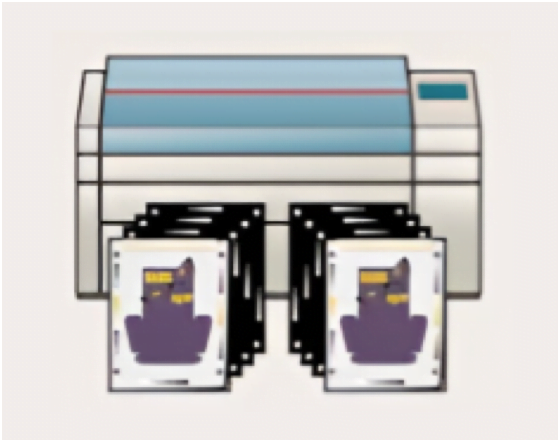
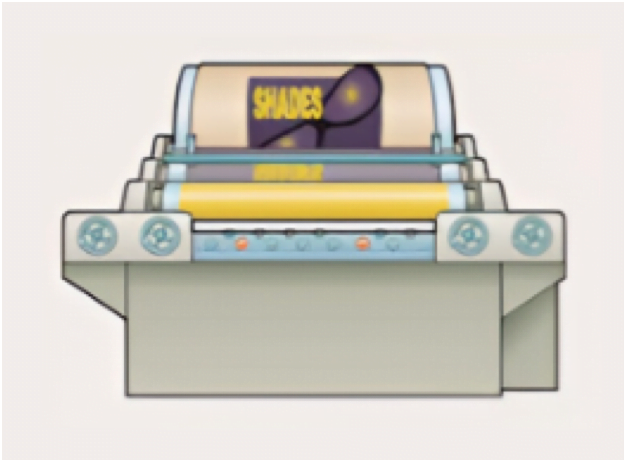
Plate Proof
Historically part of plate mounting for wide web flexo presses, plate proofs verify register accuracy and content quality but seldom match press colours accurately.
Printing Press Proof
Printing press proof, the most accurate but costliest proofing method, is printed on the press itself.
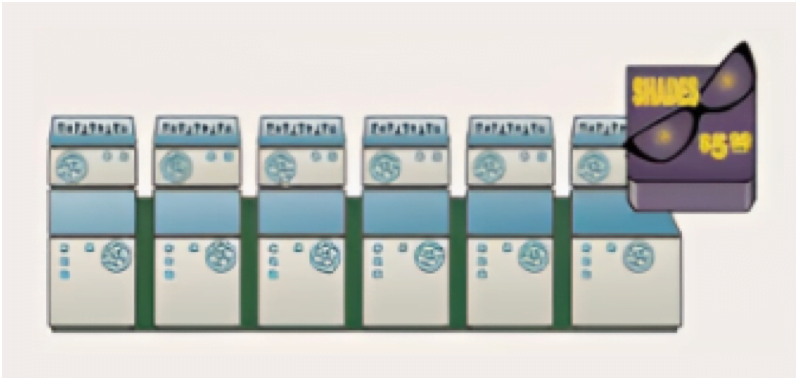