Flexo printing, known simply as flexo, has become an indispensable printing technique, favoured for its versatility and efficiency. As with any sophisticated process, a thorough understanding of the underlying consumables is essential for bespoke printing applications. This article will guide you through the key consumables in the flexo printing process to help you make your decision.
Key Consumables in Flexo Printing Process
Choosing the right combination of inks, inking units, plates, mounting tapes and substrates can make a world of difference in the quest for print perfection.
Flexo Inks and Their Evolution
The inks are at the heart of the flexo process.
- Solvent-based inks, favoured for their fast drying times, are often chosen for packaging materials that require fast production cycles.
- Meanwhile, water-based inks, praised for their reduced environmental footprint, have grown in popularity as a result of increased environmental regulations and consumer awareness.
- UV inks complete the spectrum with their near-instantaneous curing under ultraviolet light, proving essential for high-end labels and packaging that demand unparalleled detail and durability.
The Heart of the System: Flexo Inking Units
Coupled with the flexo inks are the inking units, of which there are two main variants.
- The separate fountain system allows precise ink control, an advantage when managing multiple print jobs that vary in ink viscosity and colour.
- The integrated chamber system, on the other hand, offers a compact design and consistent print quality, thanks to an enclosed environment that minimises contamination and evaporation.
Flexo Printing Forms: The Image Carriers
The image carriers in flexo, the printing forms, come in a variety of forms.
- Photopolymer plates are popular for their accurate image reproduction and ease of production, offering a flexible solution for a wide range of printing tasks.
- For high-volume or continuous runs, elastomer sleeves come into their own; their impressive resilience and ability to minimise downtime cement them as a staple for large-scale operations.
Choosing the right foam tape for plate mounting is no small decision in achieving the desired print quality. Suppliers typically offer a range of foam tapes with different hardnesses to suit the specific requirements of the job, whether it’s precise screen work, robust solid fills or intricate line work on a variety of substrates.
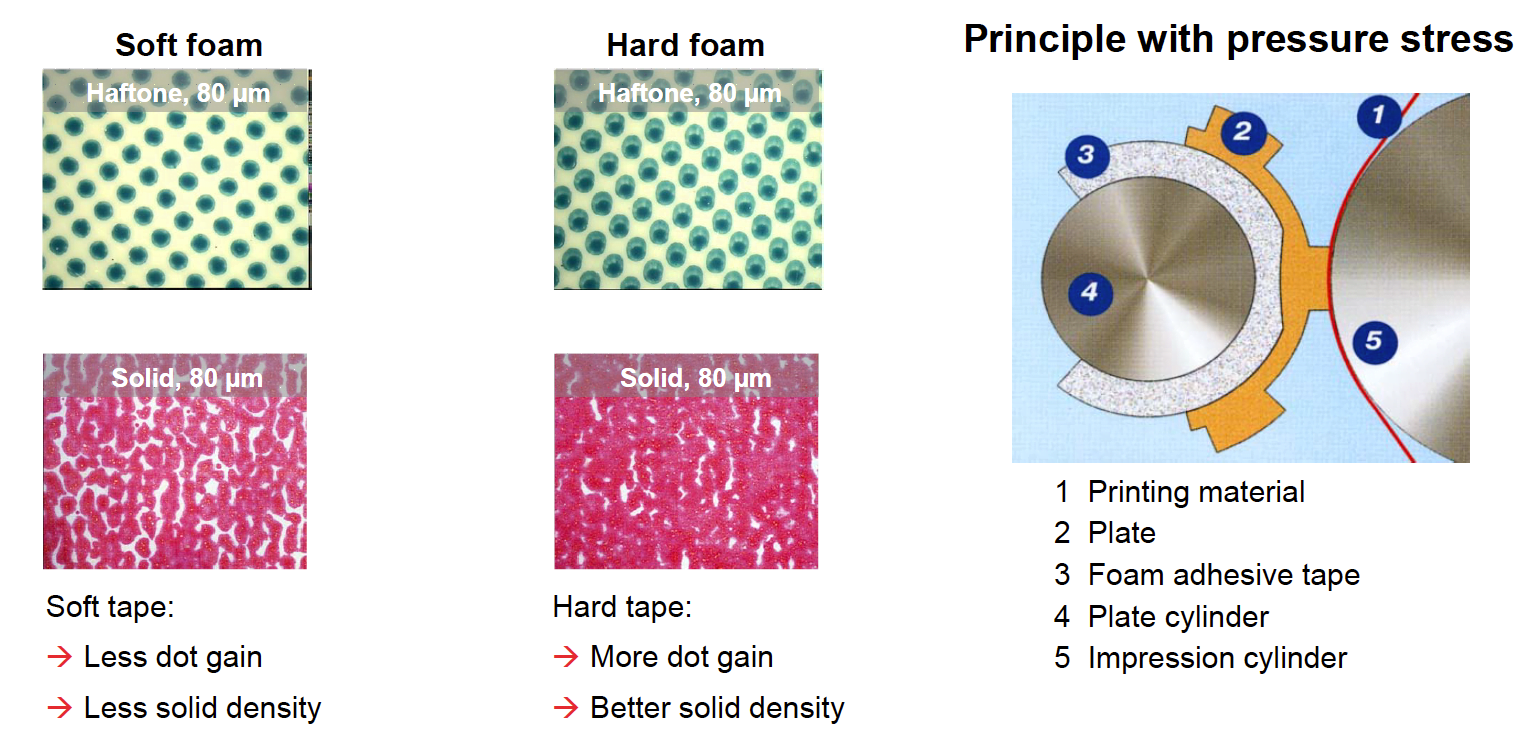
The right tape hardness, coupled with appropriate thickness options such as 0.10mm, 0.38mm or 0.55mm, facilitates optimal ink transfer and accommodates substrate surface irregularities. Soft tapes can cushion the print for bold solids, while harder tapes provide the firmness needed for fine detail, creating the perfect cylinder-tape-plate “sandwich”.
The Underrated Players: Flexo Mounting Systems
Mounting systems are the unseen heroes in achieving high quality prints.
- Choosing the right mounting tape is critical – it ensures that plates are securely attached to the impression cylinder, providing consistent print quality.
- Cushioning foams absorb shocks and vibrations during printing and promote a smooth print surface.
- For sleeve-based systems, the use of pneumatic and hydraulic bridge adapters is key. These adapters accurately align sleeves on the press, eliminating minute misalignments that could otherwise compromise print integrity.
Substrate Versatility: The Canvas of Flexography
Flexography’s adaptability shines through when printing on different substrates, each with its own unique characteristics.
- Paper, from coated to uncoated, has a different aesthetic and tactile feel that reflects the essence of a brand.
- Corrugated materials, varying in their combination of flutes and liners, bring structural durability to packaging.
- The extensive range of films – including PE, PP, PET, PVC, nylon and aluminium foil – meets the demand for flexible packaging with varying barrier properties, making careful substrate selection essential.
Film
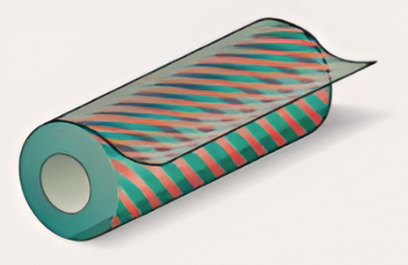
- Polyethylene (PE, LDPE, HDPE)
- Polypropylene (PP, OPP, BOPP)
- Polyester (PET)
- Polyvinylchloride (PVC)
- Nylon
- Aluminium foil
Conclusion
The flexo printing process is a symphony of precision elements, with each sort of consumable playing a crucial role in the outcome. An intimate knowledge and careful selection of inks, inking units, printing forms, mounting systems and substrates is what transforms good prints into exceptional ones. As the industry’s horizons expand, the expertise of practitioners in choosing the right variants will continue to underpin the ever-evolving tapestry of flexographic printing – a testament to the blend of creativity and scientific precision in this dynamic field.