What is the need of solvents for flexographic printing plates?
Flexography uses „standing“ printing elements to carry the ink towards the substrate. The raw flexo printing plate, which means without the printing image, is supplied in a sheet form which is precisely extruded to it final thickness by the printing plate manufacturer. After imaging, the plate gets cured with UV light to cross link the photopolymer in the areas which should later print. The other areas should obviously not print and need to be removed.
For removing the excess uncured photopolymer three different processes are used. They are commonly described as solvent -, water – and thermal processing. The solvent process is yet by far the most common one as it is very versatile and all kinds of different plates, in particular, different thicknesses can be used. Repro houses or trade shops mainly make use of the solvent plate processing technology as it allows them to manufacture thin plates (1.14 – 1.70 mm) for flexible packaging or label applications and with the same washout device also thick plates (3.94 – 6.35 mm) for corrugated applications.
What is the purpose of the solvent?
The solvent is used in the plate washer. The plate washer is used to „clean“ the plates from the exceed photopolymer. The solvent thereby acts as the agent to dissolve the uncured photopolymer. At first it is either sprayed or applied through brushes onto the printing plate. The solvent then dissolves the polymer and the brushes remove it. After the washing cycle the plate is dried to remove the solvent which has been soaked up by the plate.
Sounds pretty straight forward, yet there are some details to it.
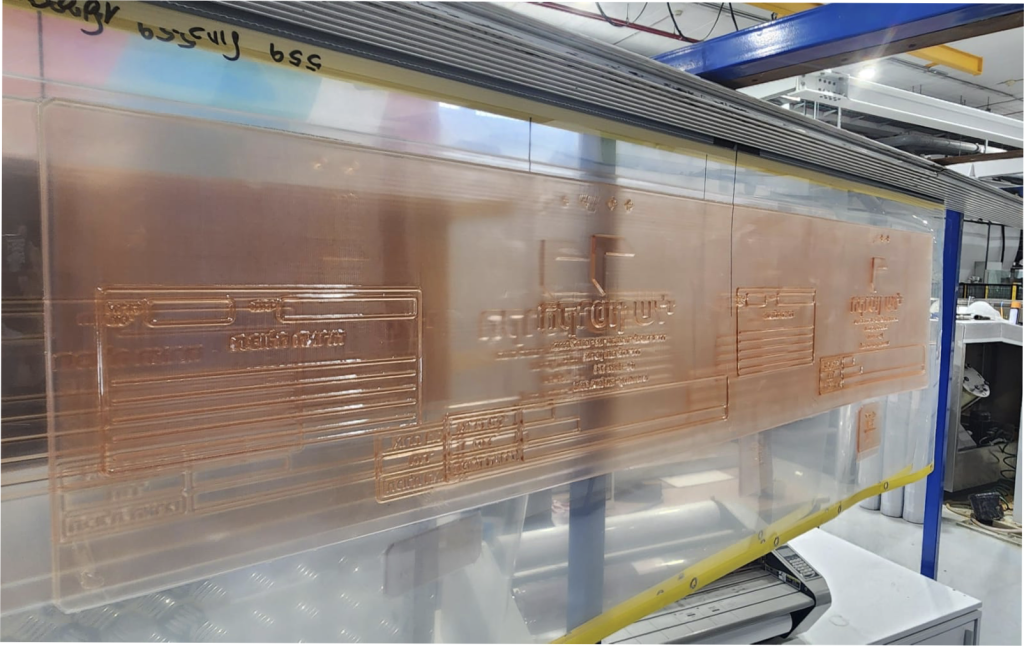
Performance and Quality
The solvent shall only dissolve the uncured photopolymer and not attack the cured areas which are the printing elements. It needs to be efficient, which means, the polymer should be removed quickly without long waiting times and last but not least, the solvent which has been absorbed by the plate need to evaporate quickly as well.
Solvent safety
Further, the solvent should not harm anyone using it in the production process and have low odour. The flash point of the solvent is ideally above 65°C for safe operation.
Re-usability
The recycling processor the wash-out solvent is often done in house with a distillation unit. The dissolved photopolymer needs to be separated from the solvent and captured which is done in said unit. The solvent thereafter should be ready to use again for further plate washouts.
Some of the flexographic plate manufacturers designed suitable solvents which manufactured by specialty chemical companies, Dupont and XSYS would be examples. Gadot for instance is a chemical manufacturer and likewise a repro house which gave them the benefit of in-house testing of their Gadsol Flexo solvent before launching it to the market.
Conclusion
Solvents are critical in the flexo printing plate process. The solvent determines the productivity process and the quality of the finished plate. It needs to be user friendly and harmless.
Typically wash-out solvents can be used for all kinds of different plates, regardless of the thickness or the brand of the printing plate. Generally the washer settings need to be adjusted when different plates are used.
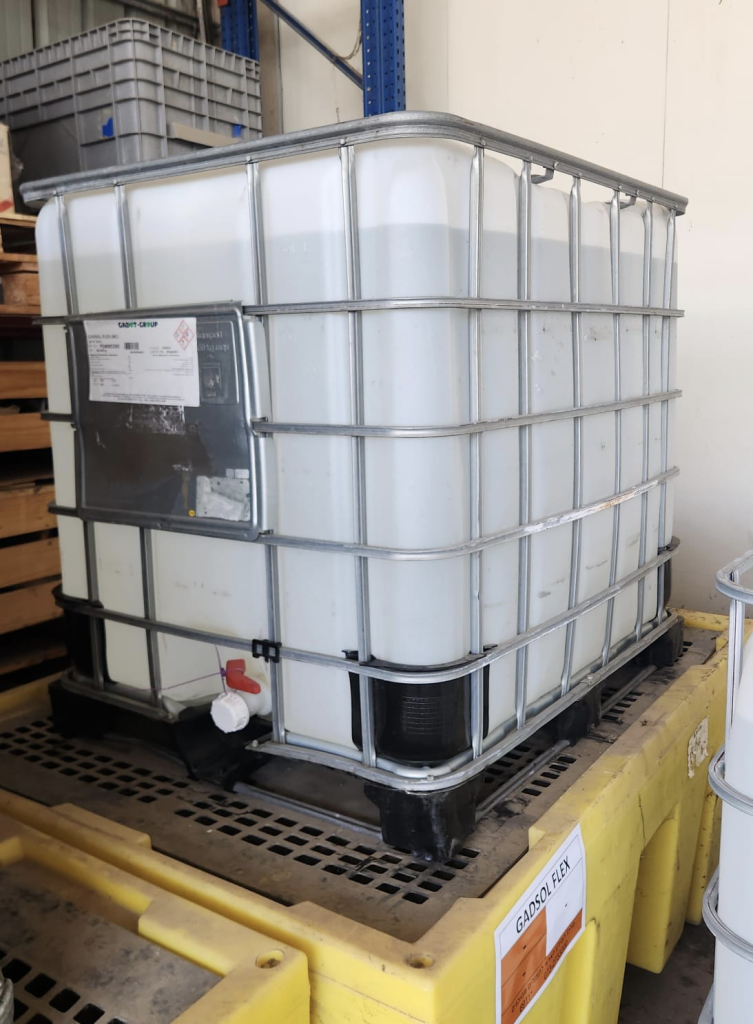